What is P material group?
Steel is defined as an alloy consisting of iron, Fe, and carbon, C, with carbon content less than 2% by weight. In addition, the properties of steel can be modified for different purposes by alloying with other metallic elements such as Chromium (Cr), Nickel (Ni), and Molybdenium (Mo) etc. for example for increasing corrosion resistance.
The ISO P classification of workpiece materials includes the metals generally referred to as steels. While steels don’t present obvious machining challenges on the level of materials such as heat-resistant aerospace alloys used in aerospace applications, steel alloys and irons are the workpiece materials most widely applied across all industries. Such wide use has spawned the development of a large selection of steel alloys with differing physical properties that generate a variety of metal cutting performance issues. Those issues, in addition to economic considerations born of high-volume production demands, make machining of ISO P steels a significant challenge for parts manufacturers as well as the makers of the tools used to machine them.
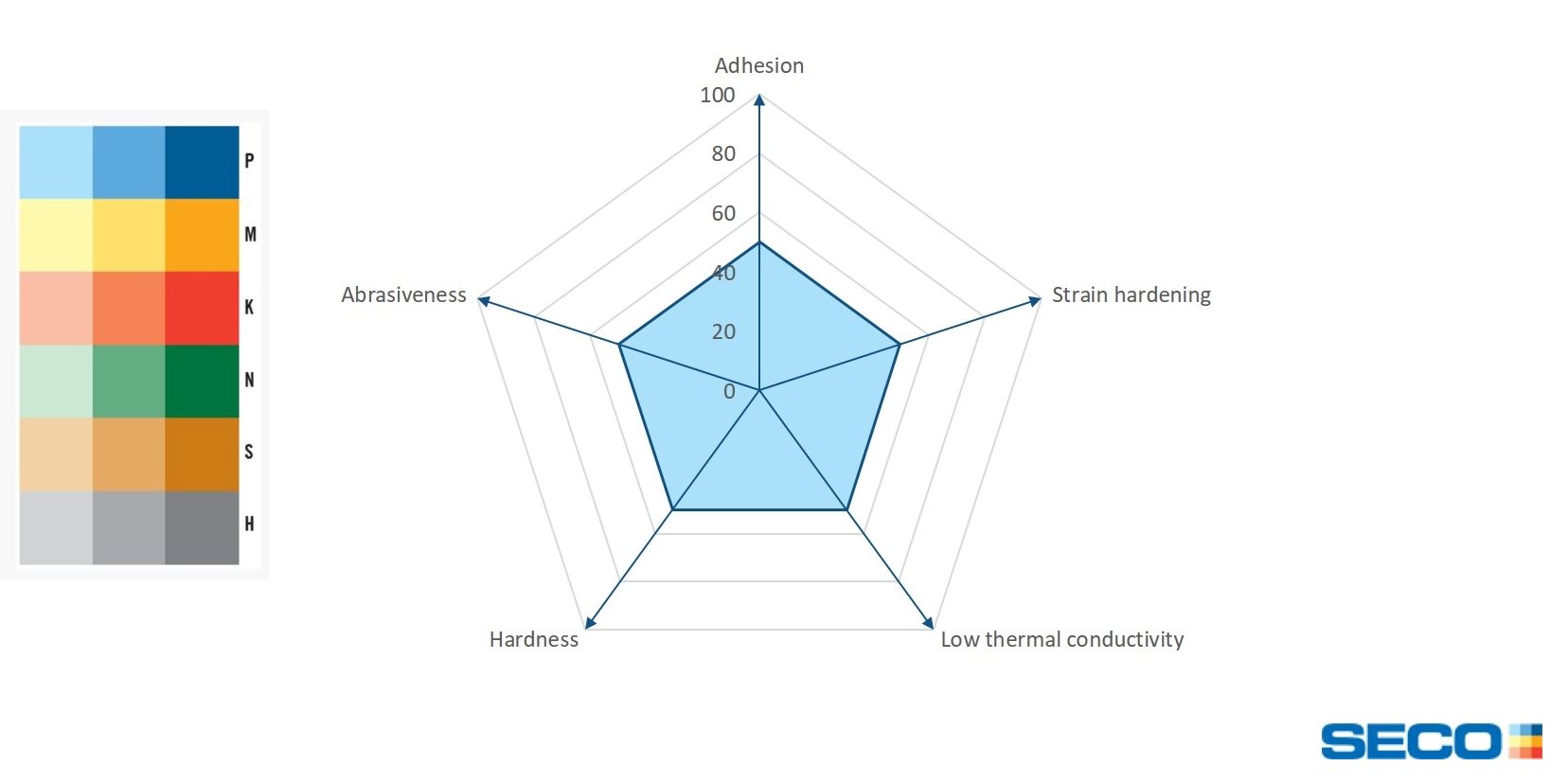
ISO P Pentagram
Seco classifies the machinability of materials based on 5 important properties: abrasiveness, ductility, strain hardening, thermal conductivity and hardness.
ABRASIVENESS, is defined as variations in hardness caused by alloying elements that are able to form hard carbide, oxide and intermetallic particles. This results in excessive wear on the cutting edges. Some examples of highly abrasive materials are Ni‑ alloys and carbon fibre reinforced plastics.
DUCTILITY, which results in adhesion and built‑up edge, refers to a high elongation at fracture for a material. This is one of the key difficulties in machining aluminiums and titanium alloys.
STRAIN HARDENING occurs when cutting hardens a surface in comparison to the bulk material. This is a well‑known challenge to overcome when machining Ni‑based alloys.
THERMAL CONDUCTIVITY refers to heat conduction of the material. The lower the thermal conductivity of a workpiece material, the more the heat will concentrate on the cutting edge, which results in excessive cutting edge temperatures.
HARDNESS is a material’s resistance to deformation. The higher the hardness, the greater the force needed to deform the material. High hardness results in high heat generation as well.
Do you want to know more about this material?
Discover our STEP program
You already have an application in mind for this material?
Find the right tool within a minute with Suggest!
Basic guidelines for machining ISO P materials, e.g. steel machining:
- High mechanical loads are your main concern (leading to flank and crater wear)
- Use big depth of cut and high feed
- Use cutting speed to balance tool life with economic considerations on the process
- Use versatile carbide grades and appropriate cutting geometry to balance with selected feed
- Emulsion (4% – 6%) cooling is advised, JETSTREAM cooling gives good results
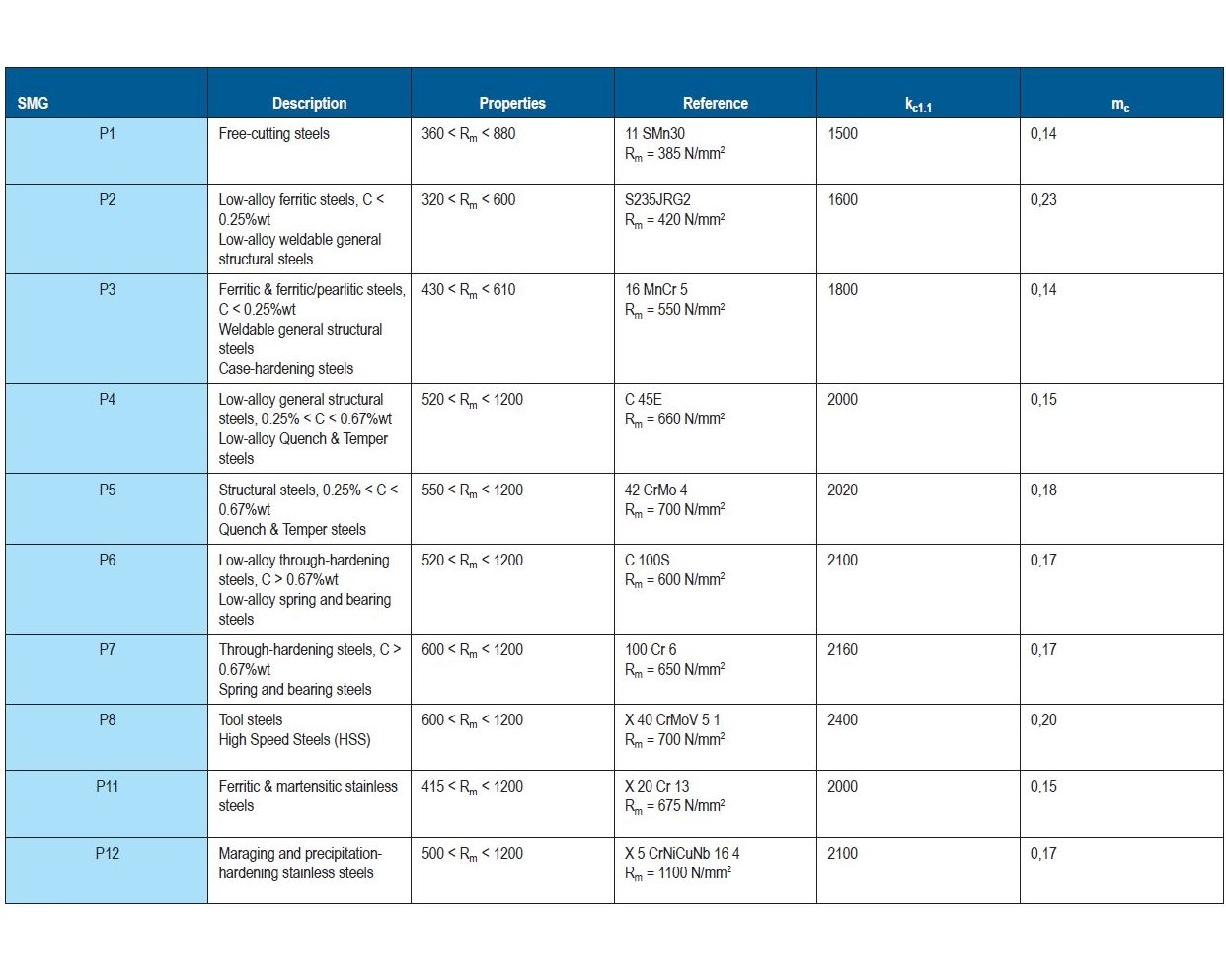
ISO P Tab extract
Inline Content - Survey
Current code - 5fce8e61489f3034e74adc64