Efficiently mill titanium and cobalt chrome implants with Seco JH724-JH726 End Mills
Learn how Seco JH724-JH726 medical barrel solid end mills provide access to machine condyle surfaces on titanium femoral knee implants.Discover the product range
Access our free Online Course on Barrel Tooling
Major medical OEMs are quickly transitioning from cobalt chrome to titanium for femoral knee implants, and those must be milled because the material cannot be ground. Manufacturers like you are now under pressure to implement machining strategies to overcome specific titanium femoral knee implant milling challenges. A cost-effective approach is the use of Seco JH724-JH726 medical barrel solid end mills with profile radii design that allow you to both finish condyle surfaces and blend surfaces with the same tool to reduce tooling costs and inventory. With large profile radii, these cutters allow for bigger stepovers while cutting at the same speeds as ball-nose end mills for shorter part cycle times and superior medical-grade surface finishes. Smaller tool tip radii provide reach into tight implant cavities.
Your challenge:
Cost-effectively mill femoral knee implants made from titanium that is impossible to grind.
The Seco solution:
Semi-finish and finish femoral condyle knee implant surfaces with one JH724-JH726 medical barrel solid end mill.
Your challenge:
Access and machine hard-to-reach patellar grooves on femoral implants.
The Seco solution:
Smaller than regular barrel tools, Seco JH724-JH726 medical barrel solid end mills are larger than ball nose end mills.
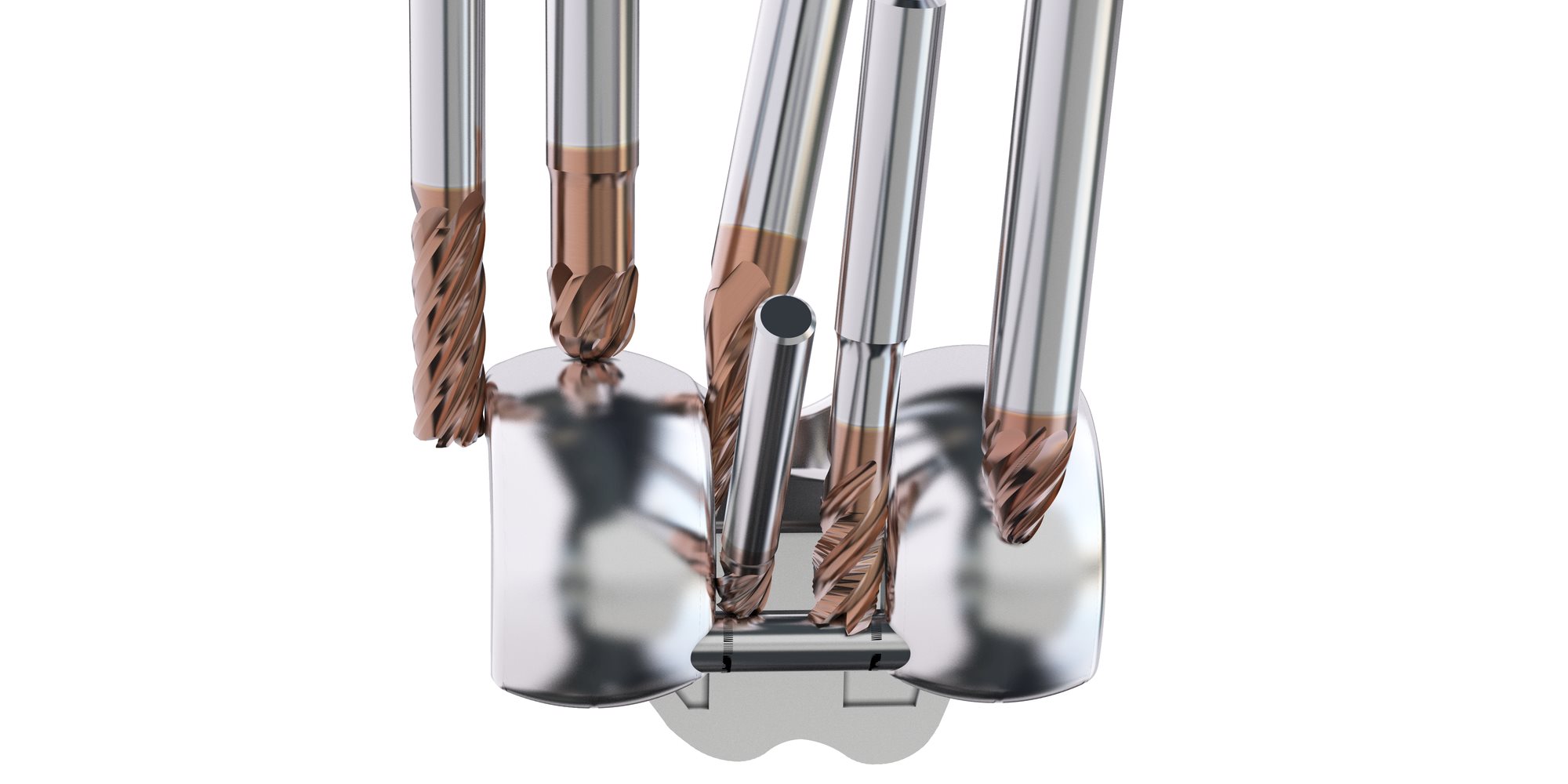
Medical implants must have perfect surface finishes. Until now, grinding has been the only way to achieve them – but titanium implants do not allow for grinding. To achieve flawless milled condyle femoral knee implant surfaces, Seco JH724-JH726 medical barrel solid end mills with multiple profile radii geometry allow you to machine main condyle surface for improved productivity, and then finish the blend radii with the same tool to eliminate any surface height deviations from tool changes and any visual transitions/imperfections on the part surface.
Your challenge:
Prevent visual imperfections on femoral surfaces from tool changes.
The Seco solution:
JH724-726 medical barrel solid end mills eliminate the need for multiple tool changes between semi-finishing and finishing operations to ensure consistently smooth part surfaces.
Your challenge:
Increase milling stepover width to shorten machining cycle times.
The Seco solution:
Special multiple radii geometries on JH724-JH726 cutting profiles allow for larger milling stepovers to prevent any visual transition marks on part surfaces.
Single-use tools have shorter overall working lives, which translates into less parts per tool and greater tooling costs that can shrink your profit margins, especially when milling titanium or cobalt chrome knee implants. With medical specific substrates, multi-radii geometries and HXT tool coatings, the reconditionable Seco JH724-JH726 medical barrel solid end mills enable you not only to reduce tooling costs and inventories, but also to lower cost per part while ensuring peak tool condition for both semi-finishing and finishing condyle surfaces on knee implants with the same tool.
Your challenge:
Amortize tooling costs as quickly as possible.
The Seco solution:
Reconditionable Seco JH724-JH726 medical barrel solid end mills allow you to machine more medical implants with less tooling inventory.
Your challenge:
Reduce scrap caused by worn tools.
The Seco solution:
Reconditioning keeps your Seco JH724-JH726 medical barrel solid end mills in top condition to generate superior milled surface finishes.
Discover the product range
Contact Us
Are you interested in Medical solutions?
Discover all our solutions and content around it
HOMERelated content
Barrel Tooling - Online Course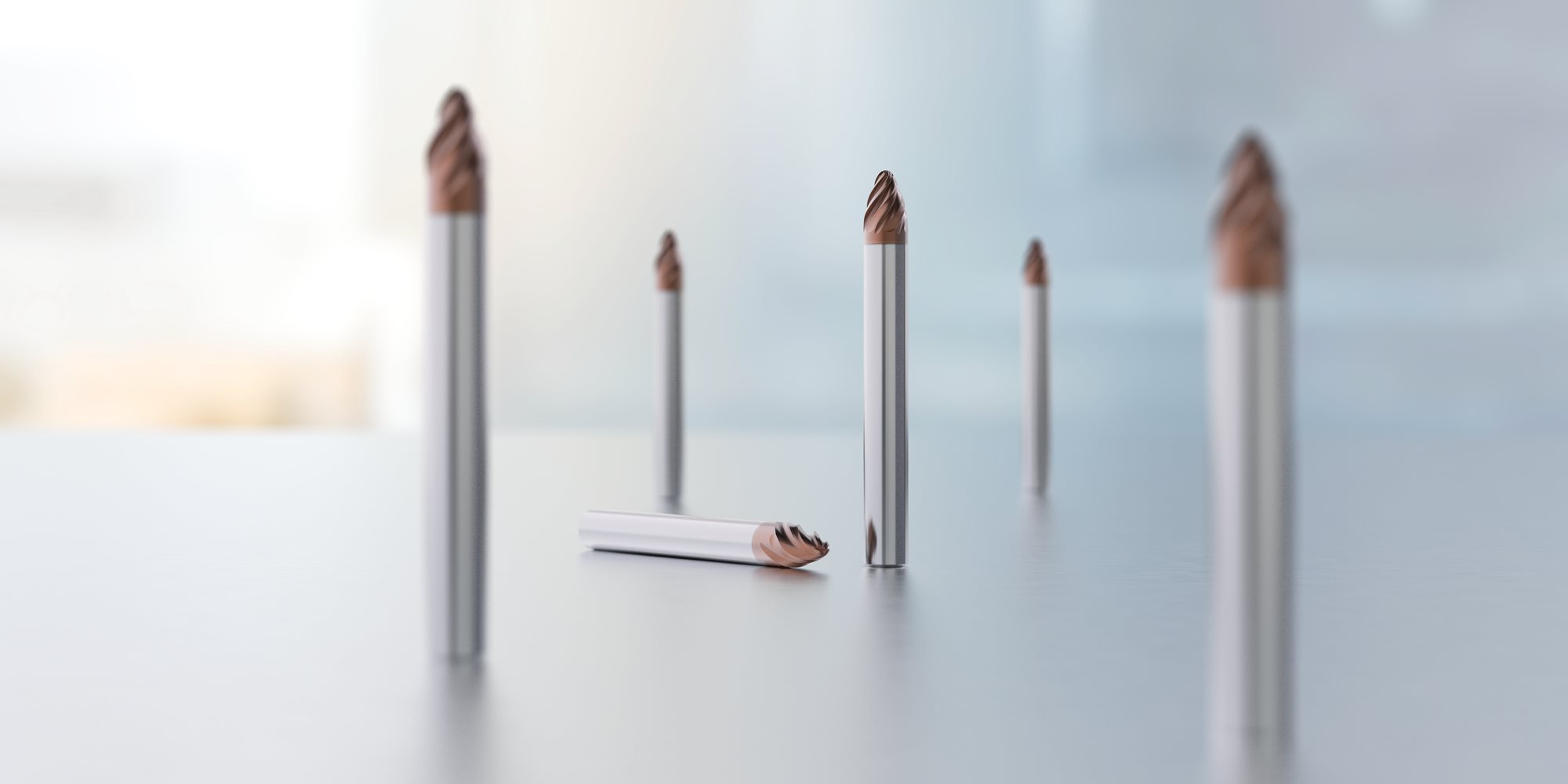
PRODUCT PRESENTATION - JH724 JH726 MEDICAL BARREL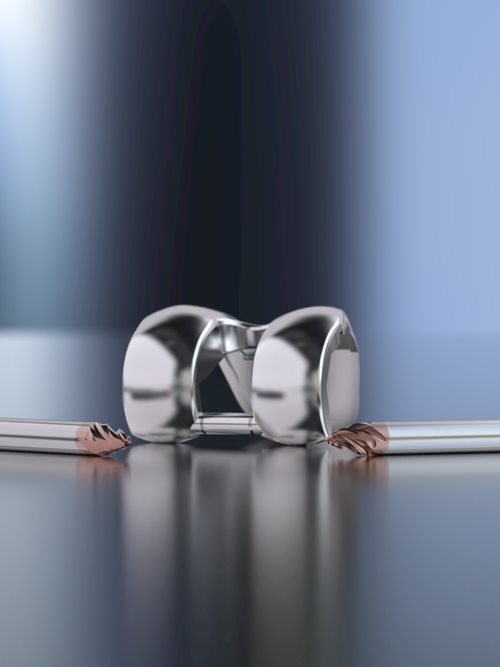
Knee Replacement Components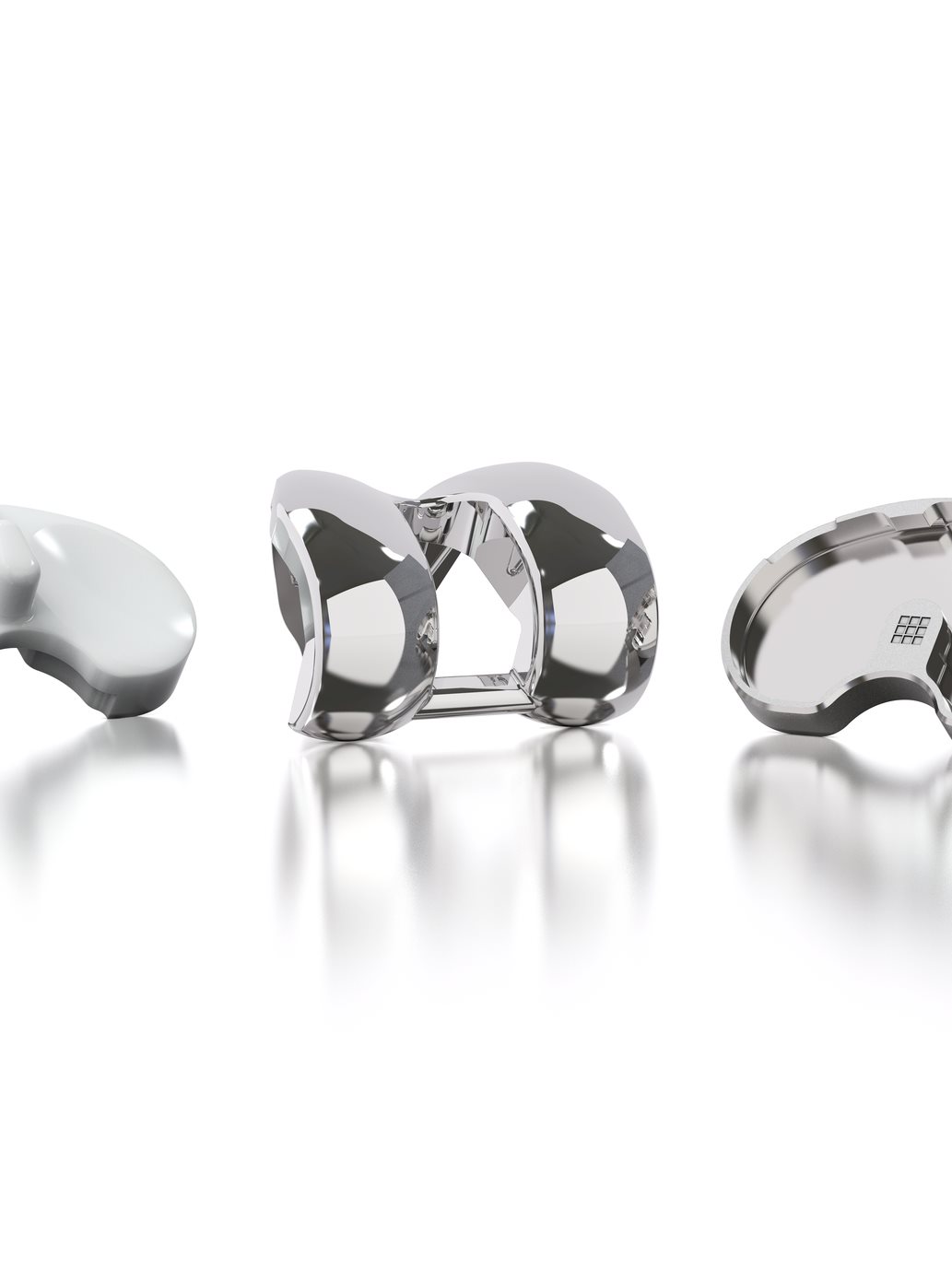
JH724/JH726 - High Speed - Taper Shape Medical - CoCr/Titanium - 4-6 Flutes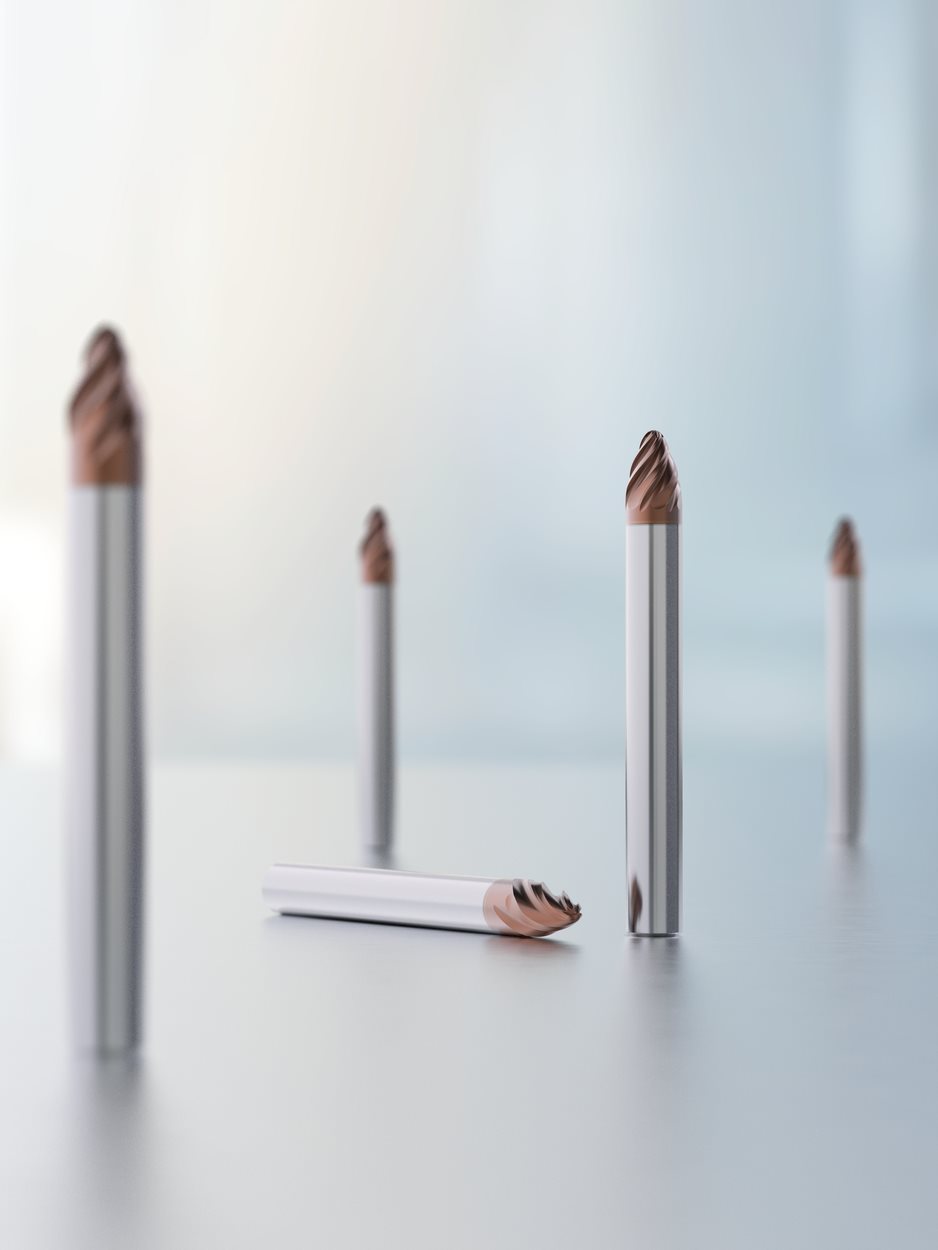
Fact Sheet JH724 JH726 Medical Barrel Solid End Mills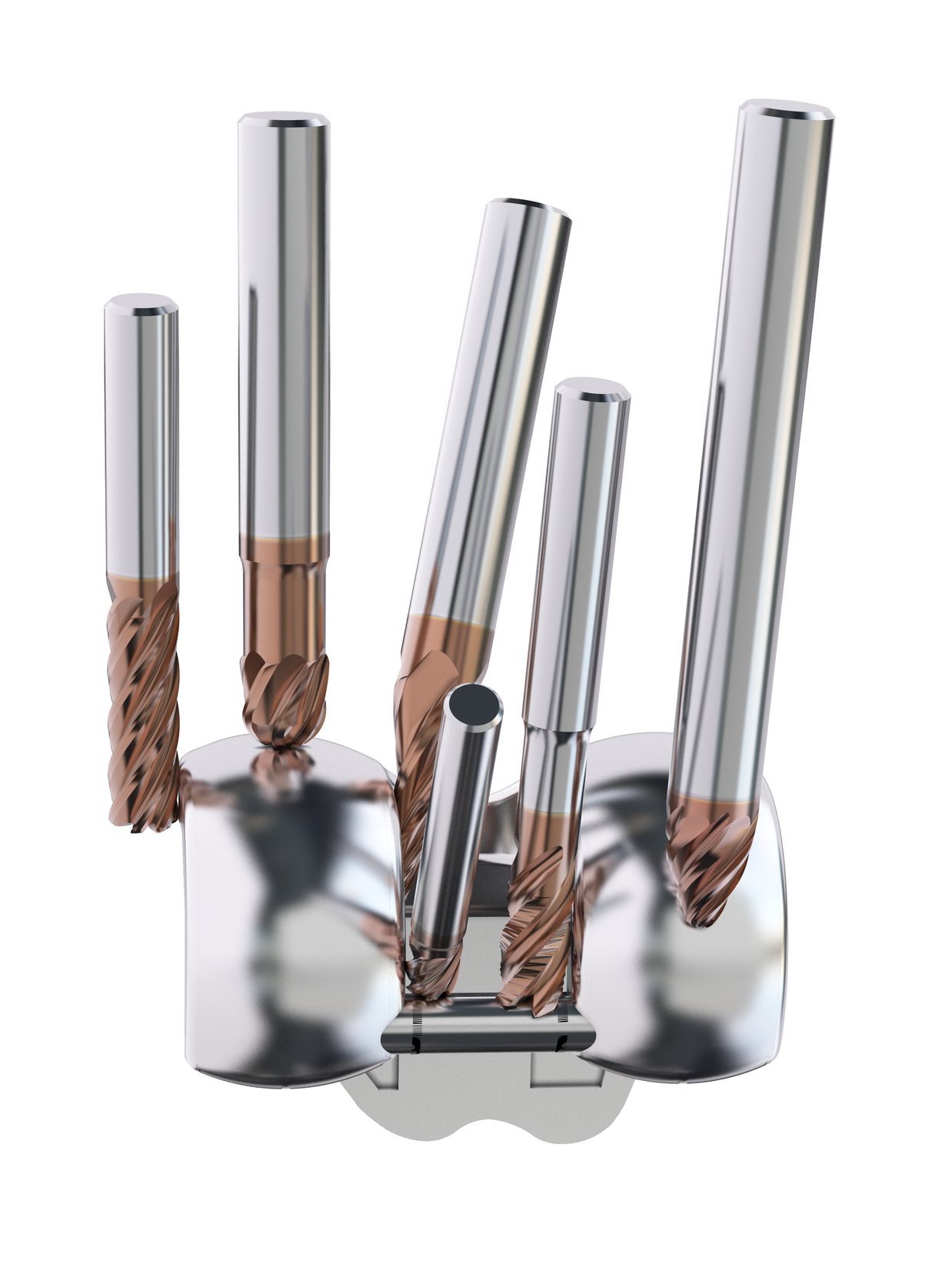
Learn more about Seco Medical Solutions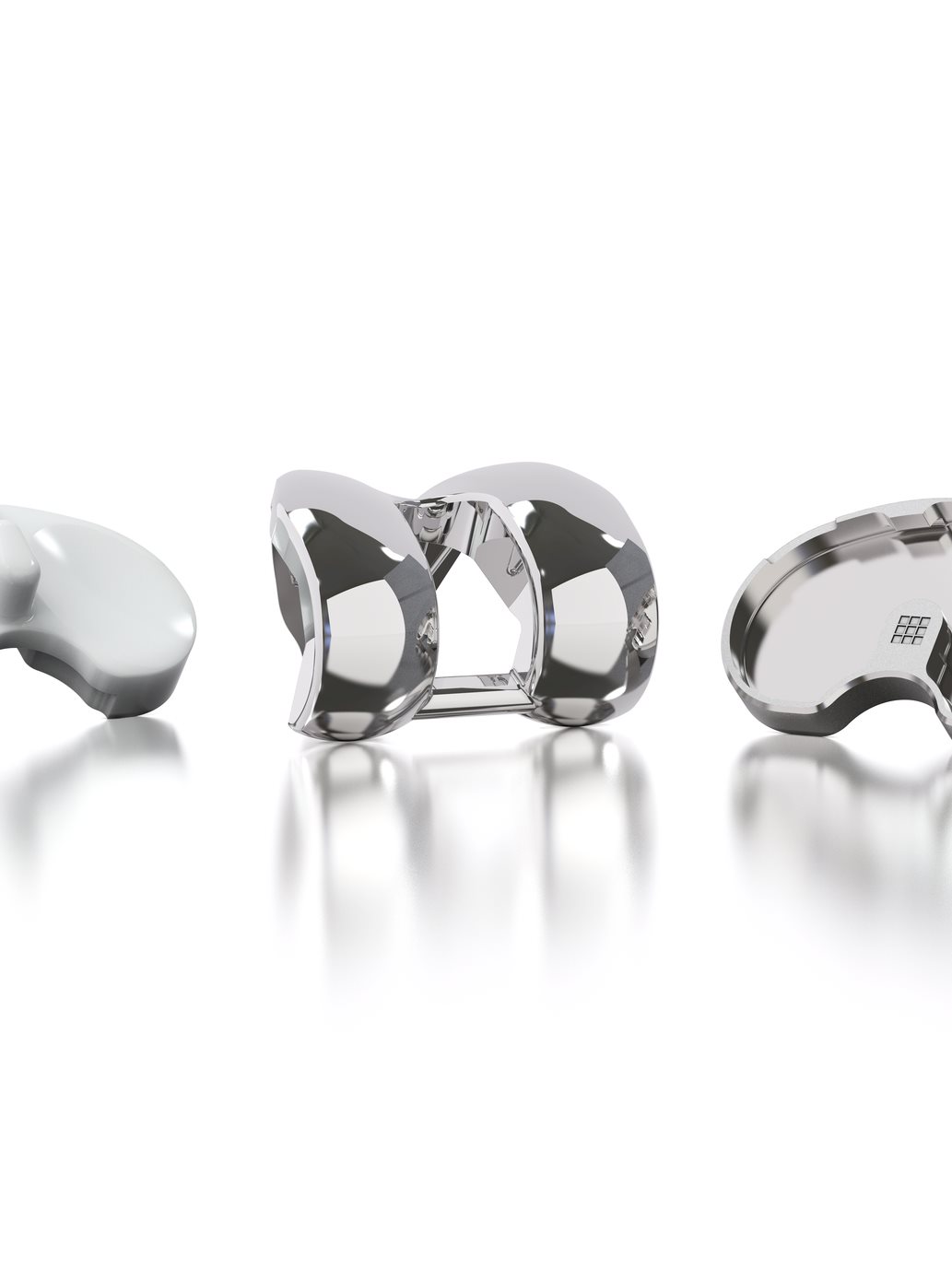
Medical Inspiration Through Innovation 2022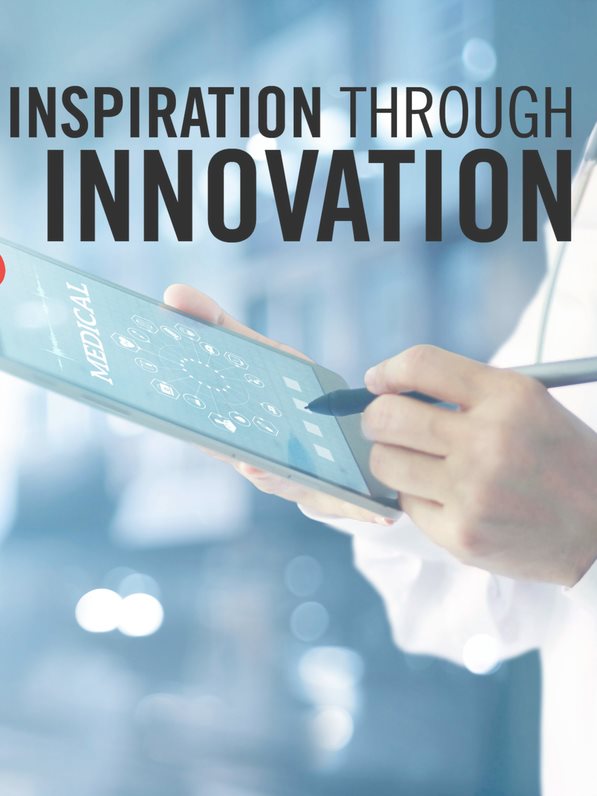
Is this the future of orthopaedics?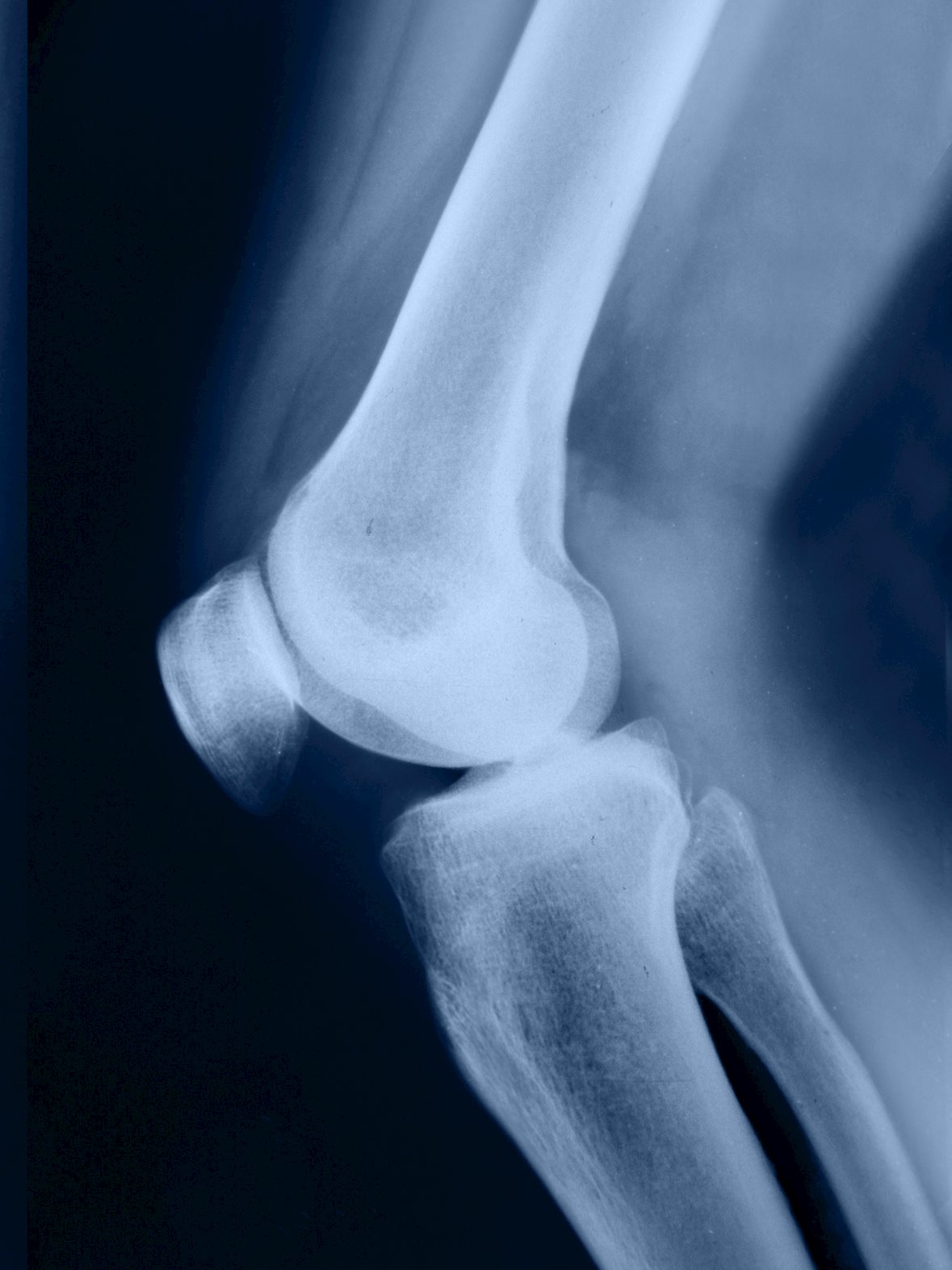
Factsheet - JH730 Solid End Mills addition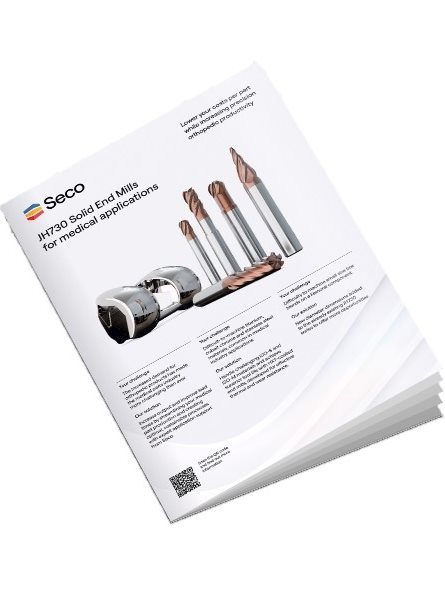
JH730 Solid End Mills addition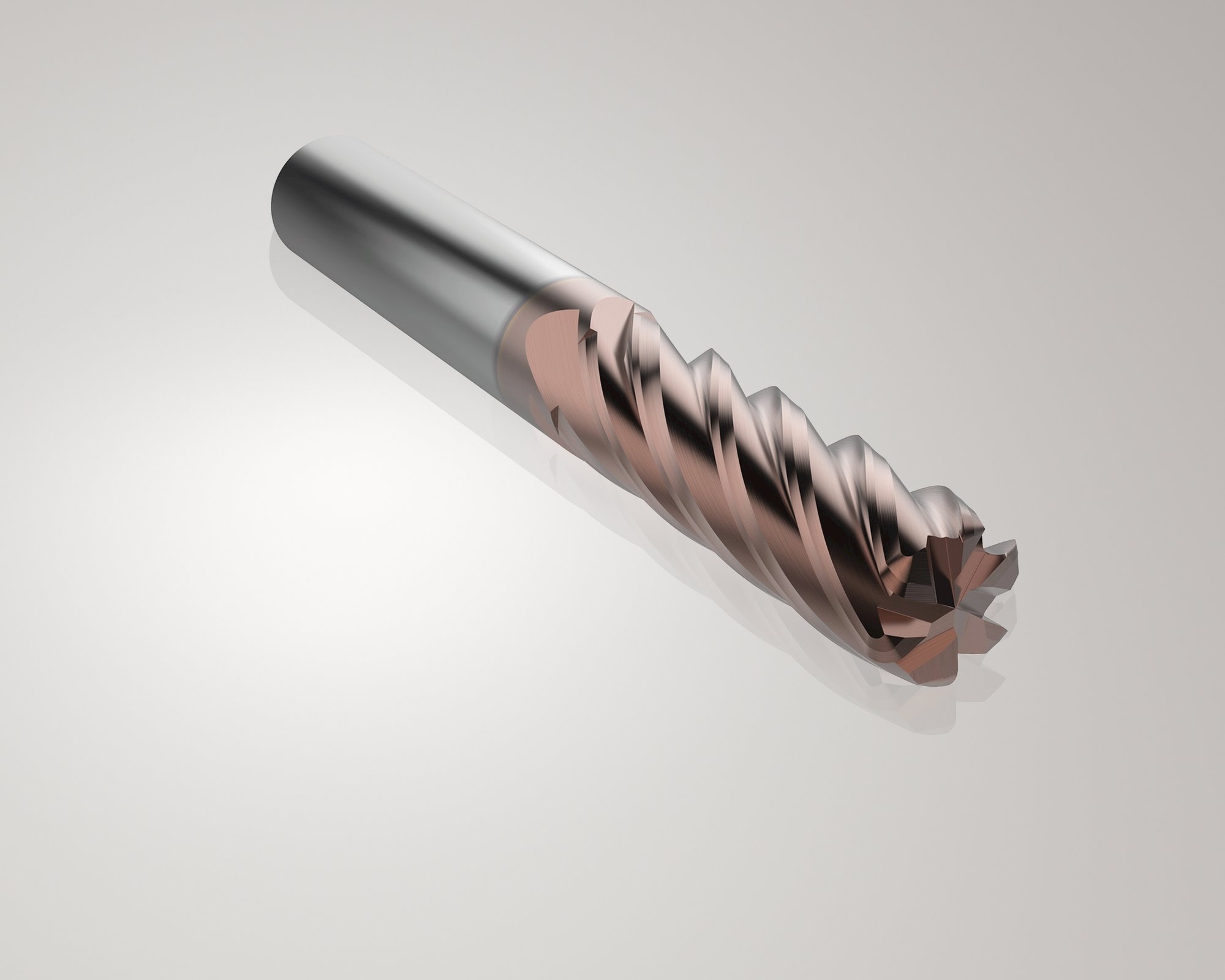
Medical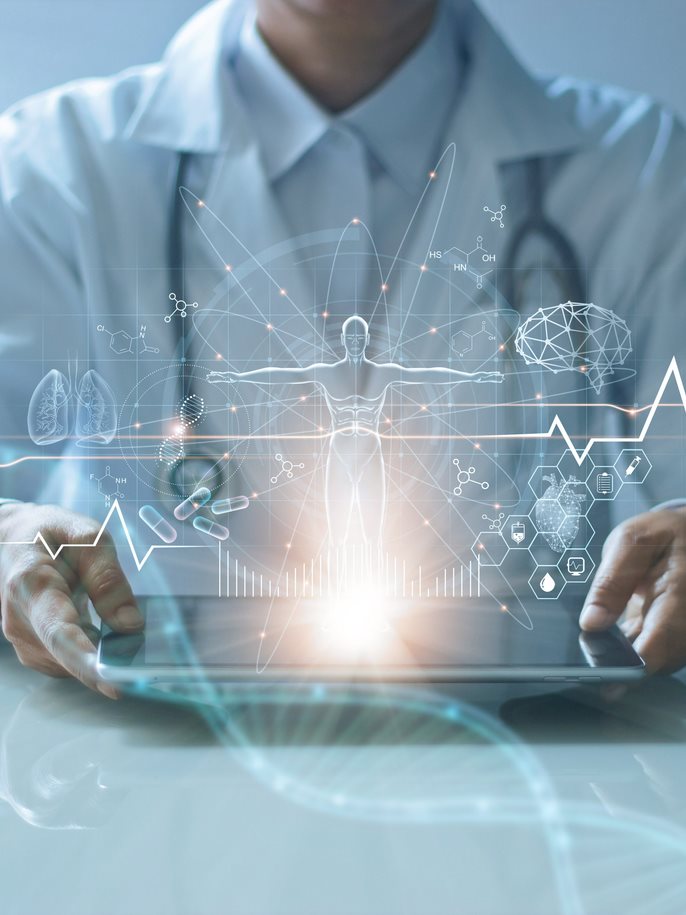
Femoral Insert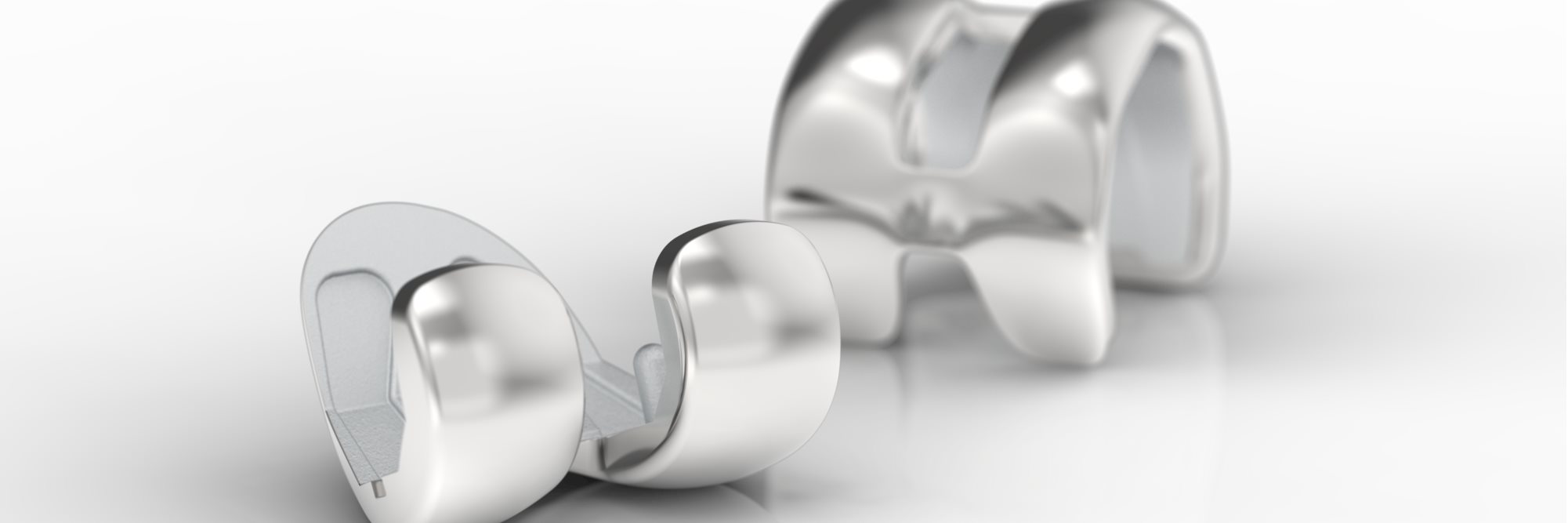
Challenges and benefits of Additive Manufacturing in the medical segment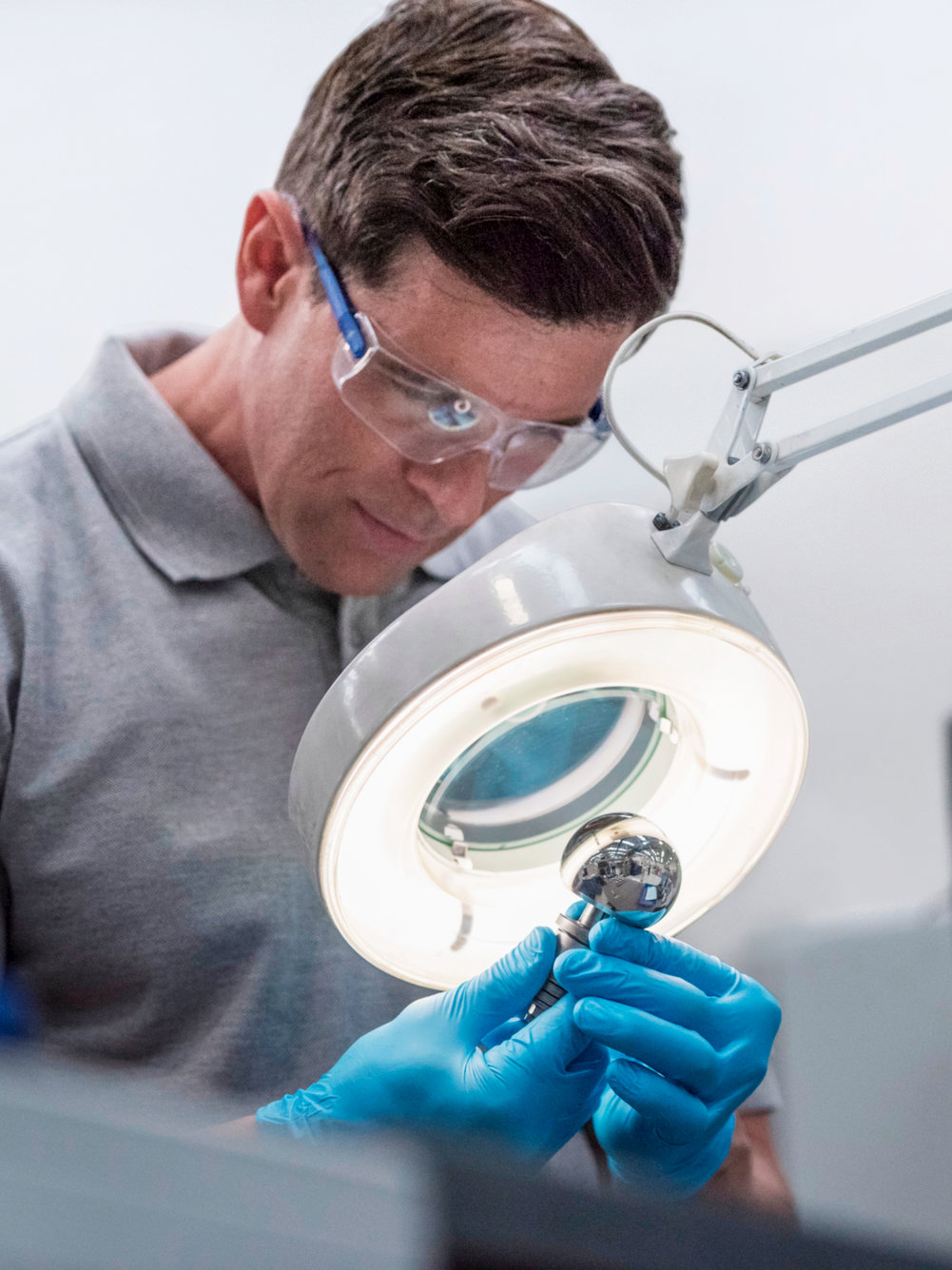
Lingering effects from the Covid-19 pandemic in the knee implant surgeries market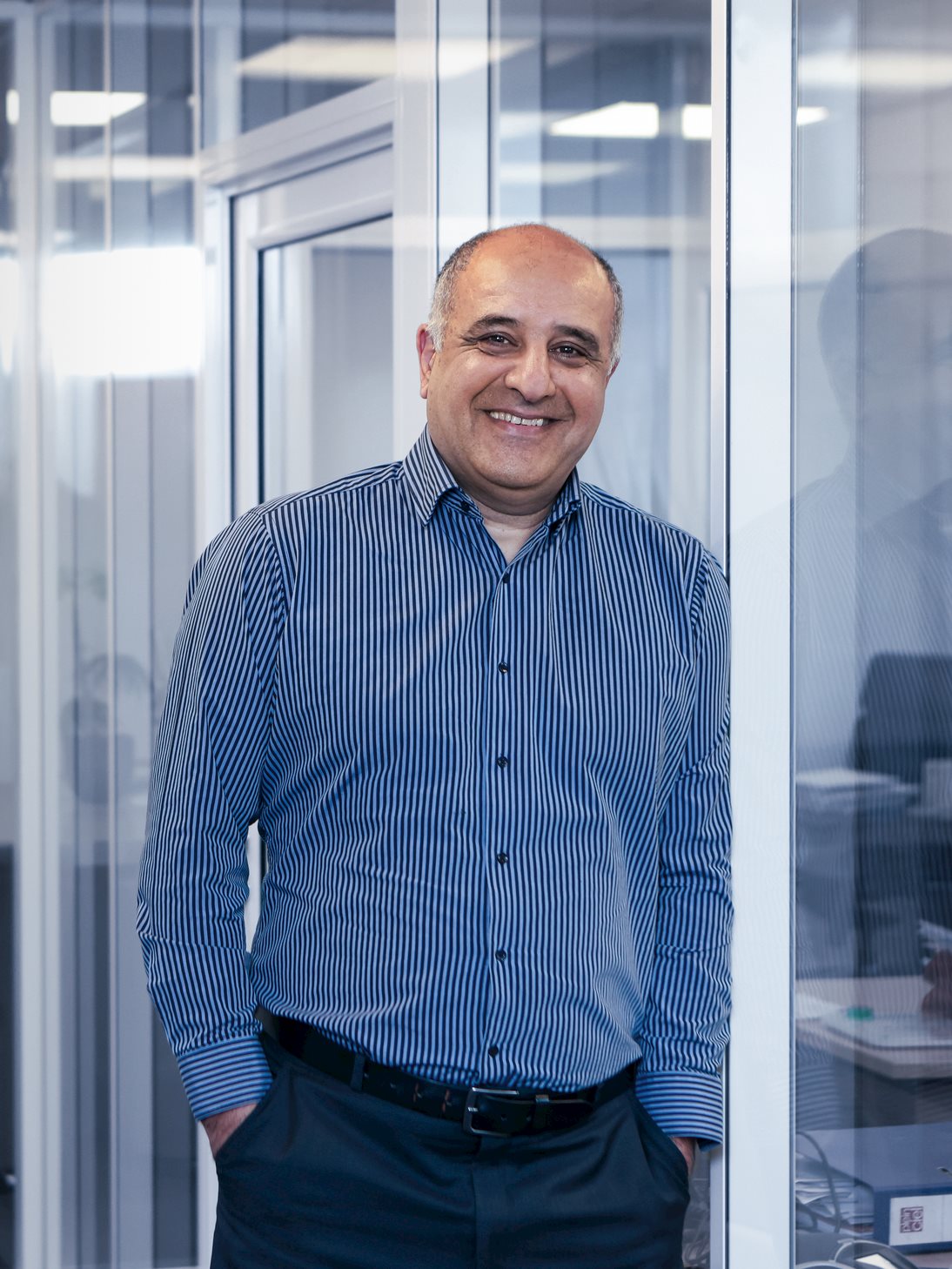
ActOn’s ‘secret weapon’ is transforming medical implants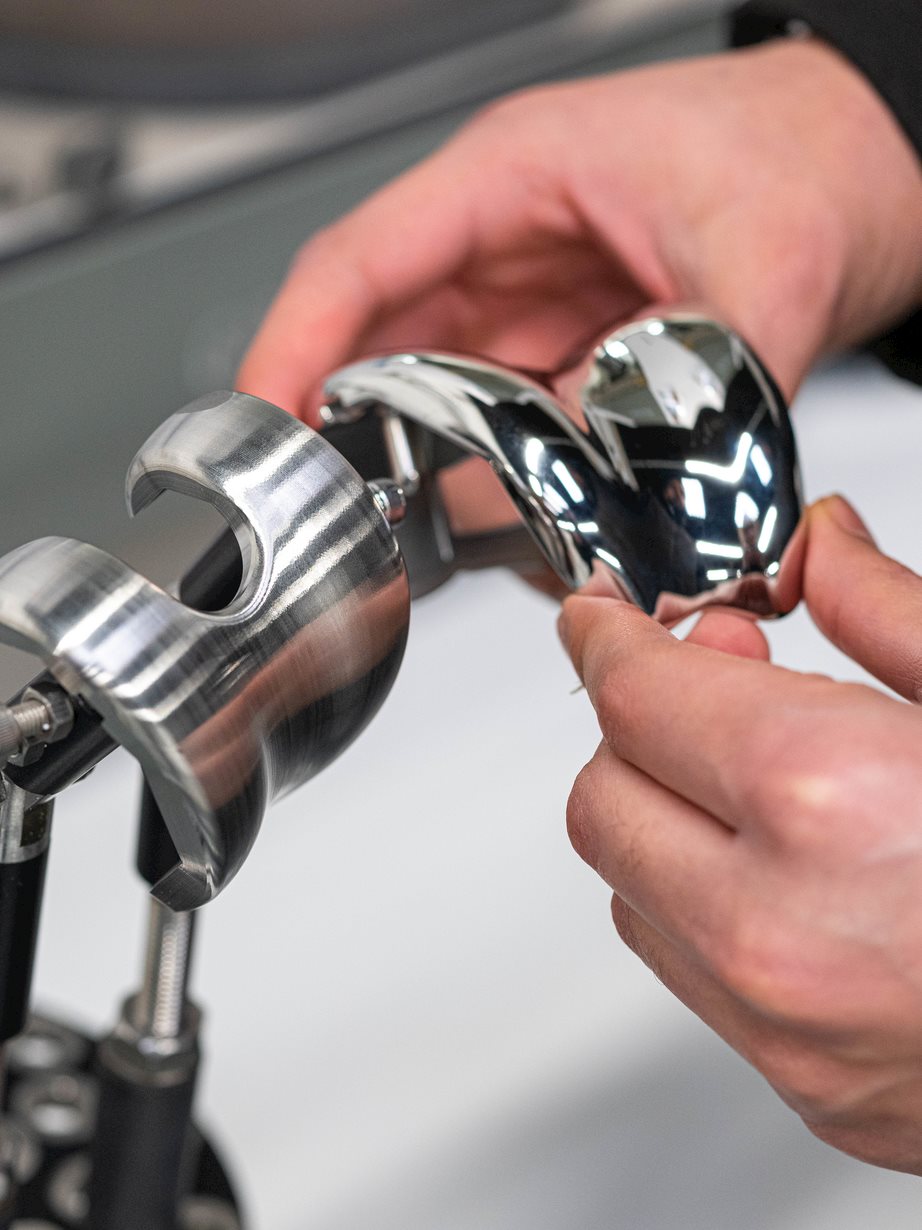
Finish Stock Allowance with Solid End Mills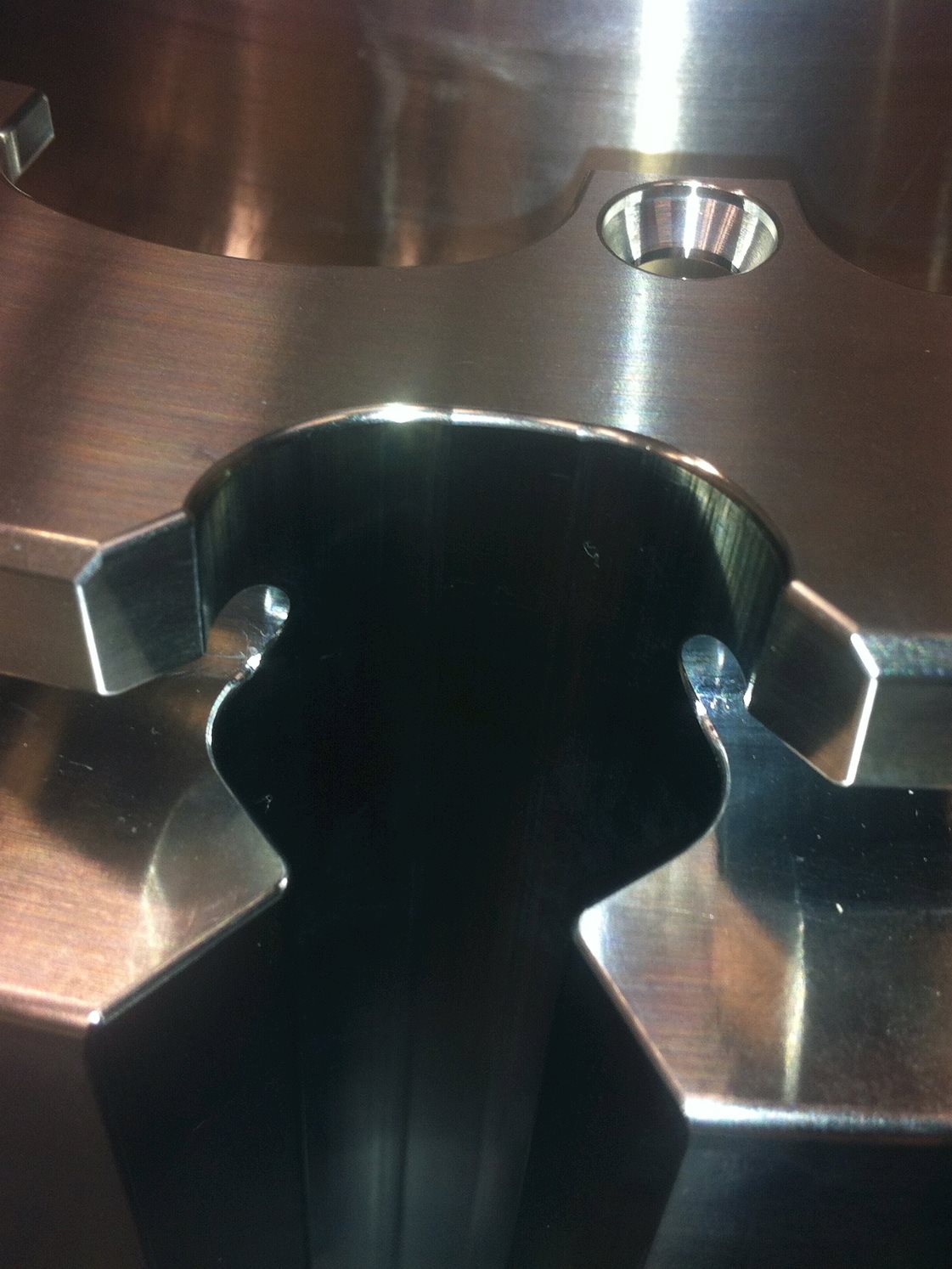
New Seco Solid-carbide cutting tools boost knee implant machining speeds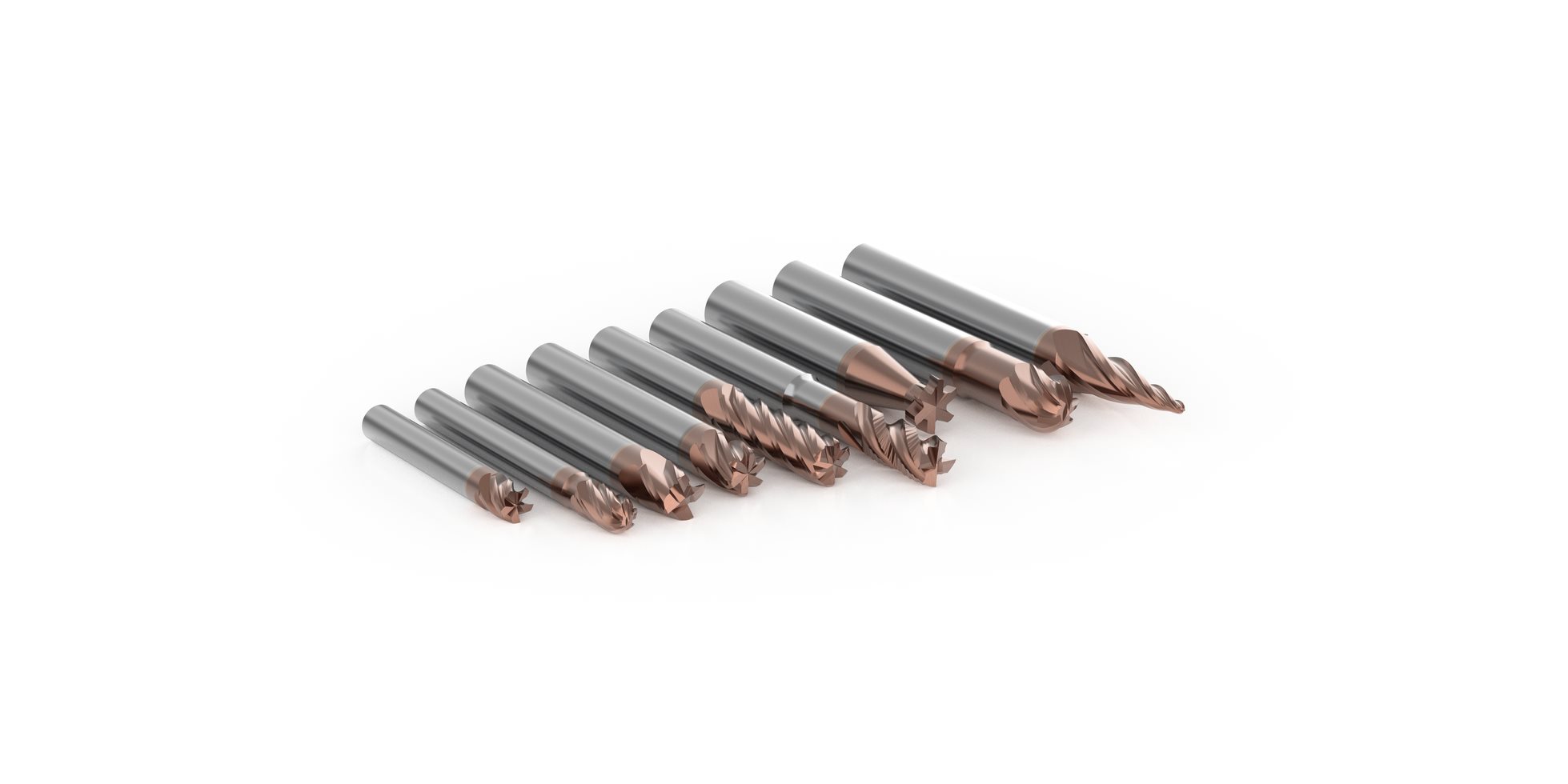
8 tips to machine titanium alloys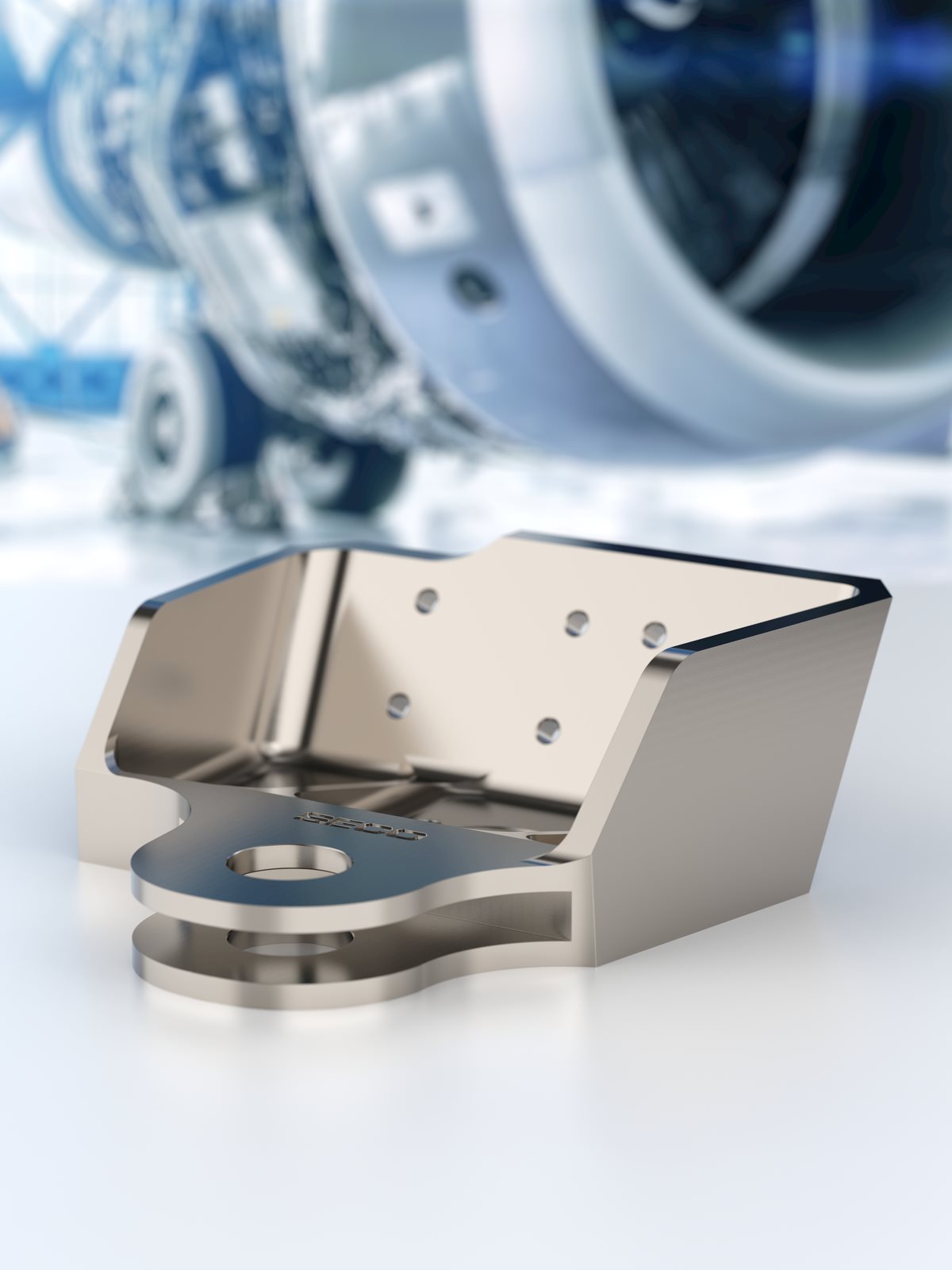
Industry-specific solutions and strategies for machining ISO-S materials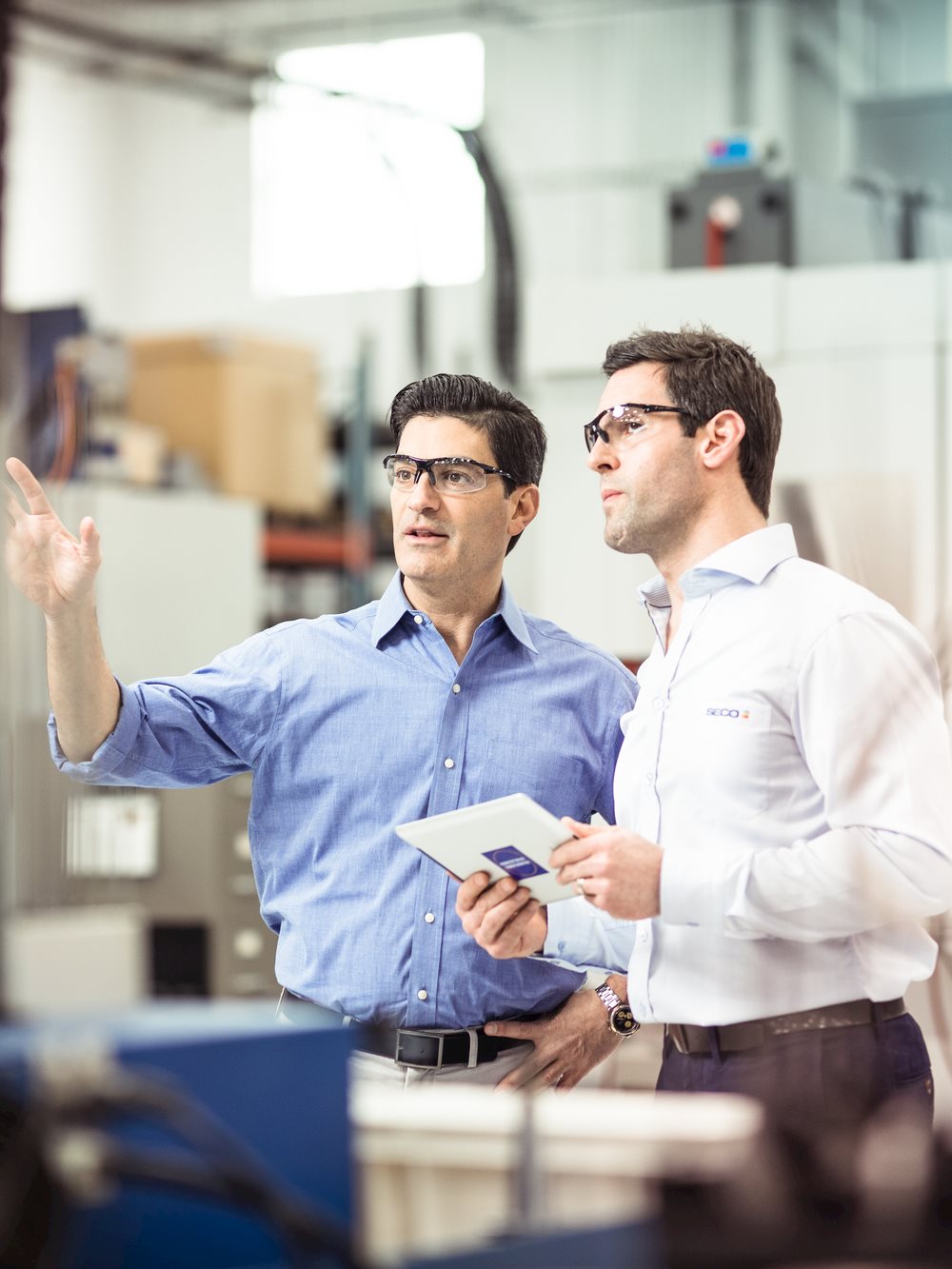
Medical Brochure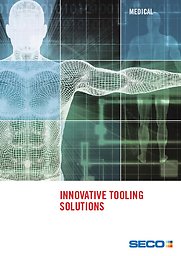
Femoral Knee Implants – a new manufacturing paradigm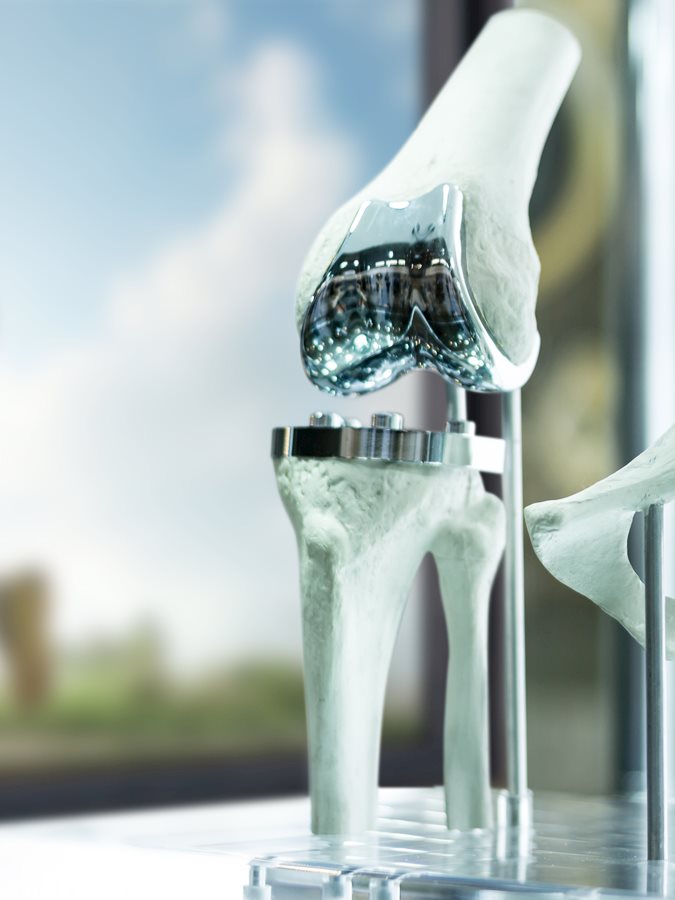
New strategies for orthopedic machining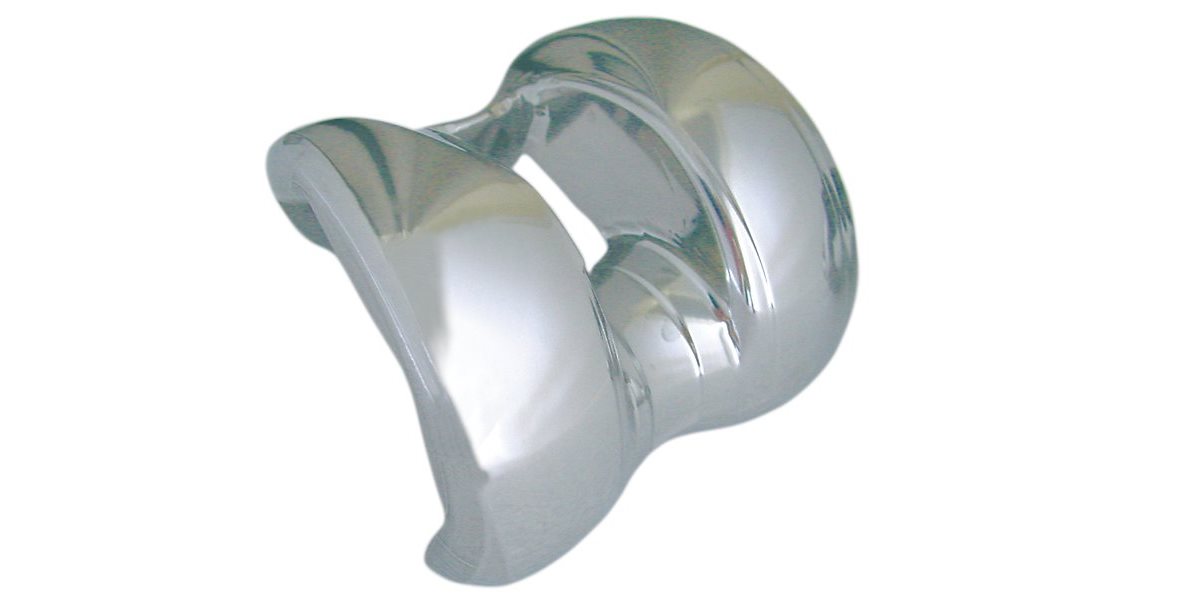
Milling tooling developments increase quality and productivity in the machining of orthopedic replacement components
Inspiration Through Innovation 2024 Aerospace and Medical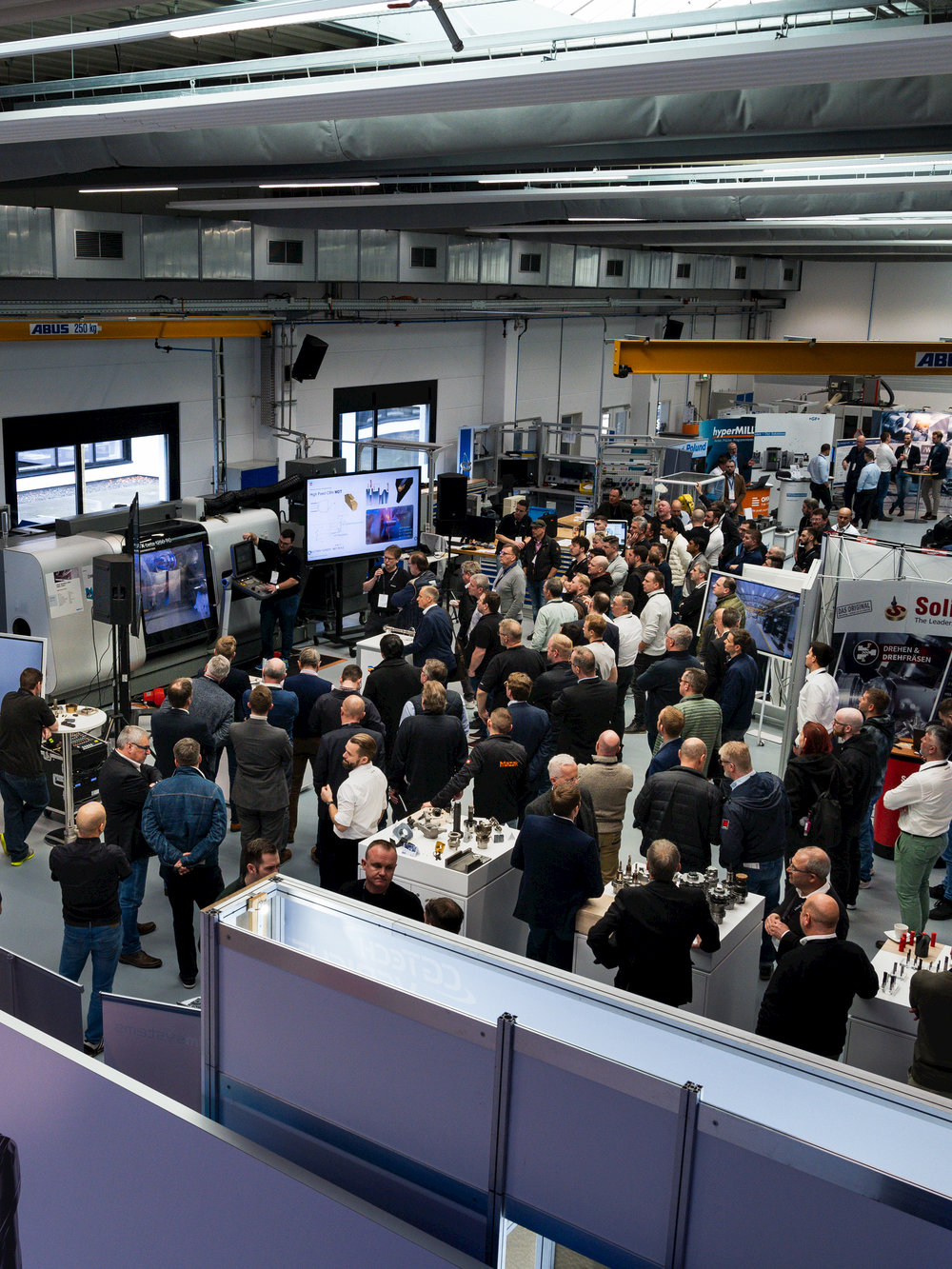
Solid Support for Additive Manufacturing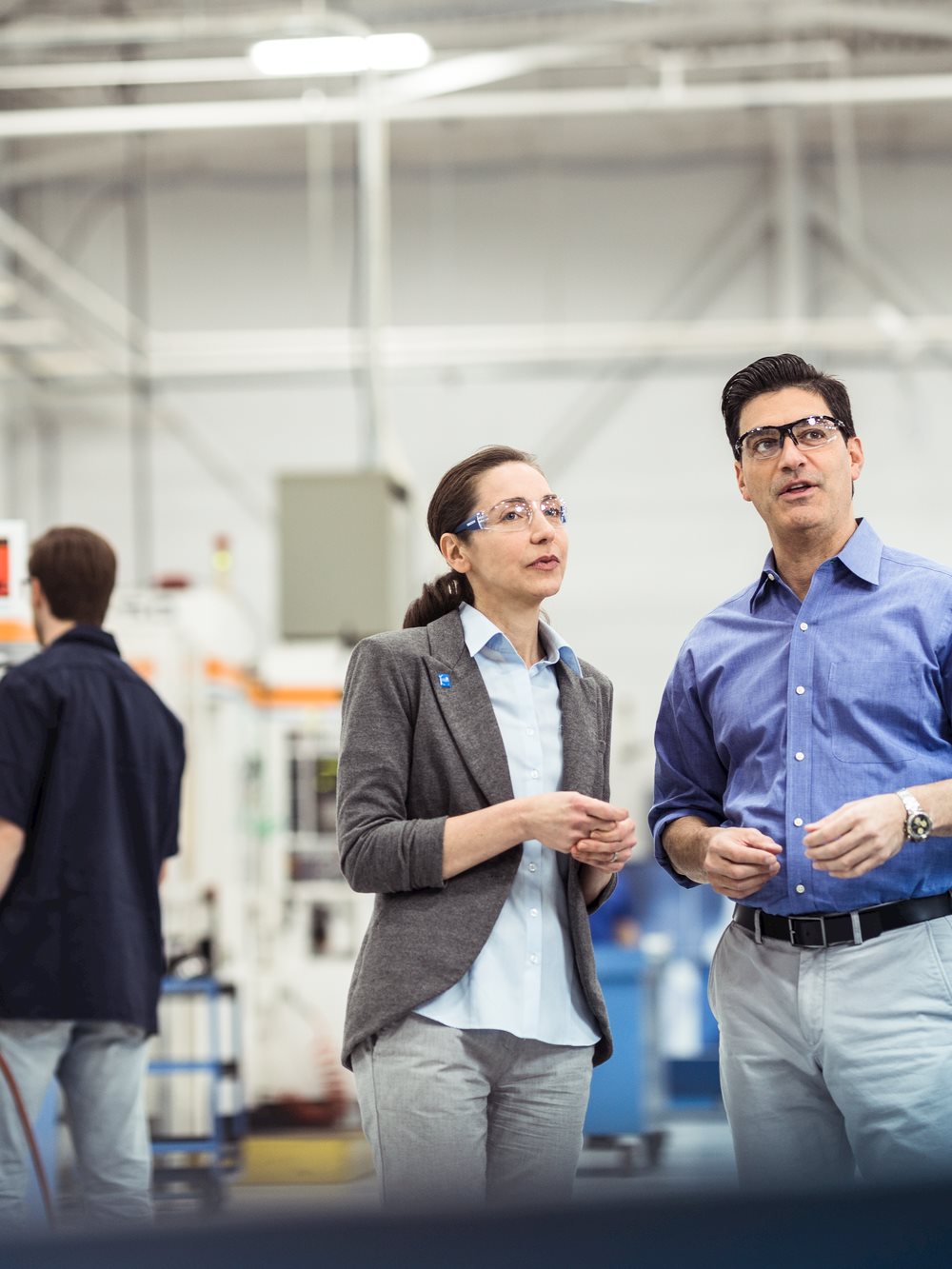
Why a Strategic Partnership is the Perfect Medicine for Permedica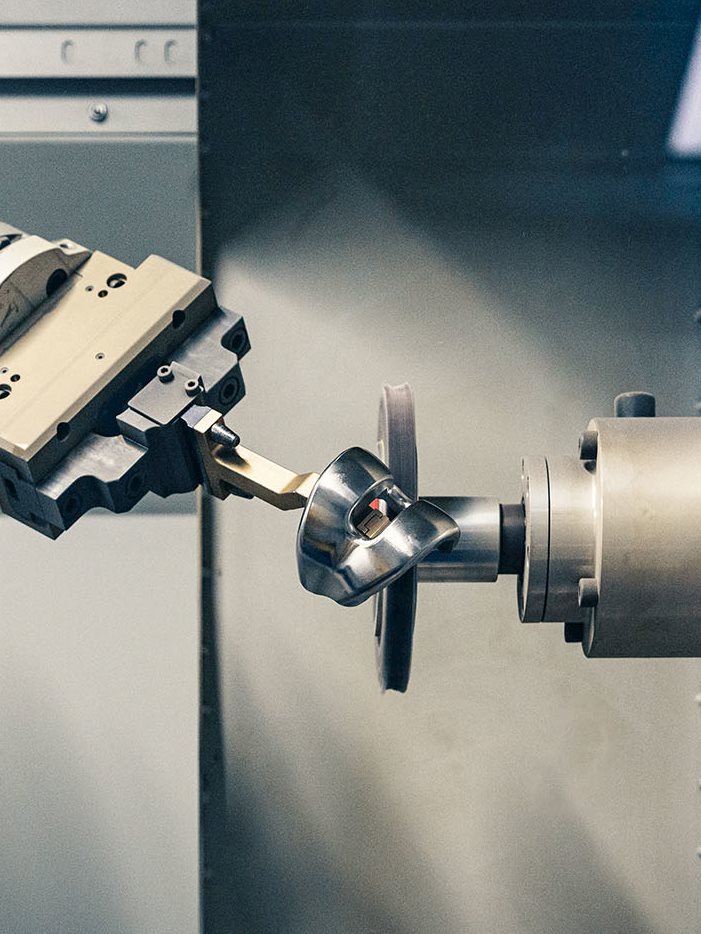
Tibial Tray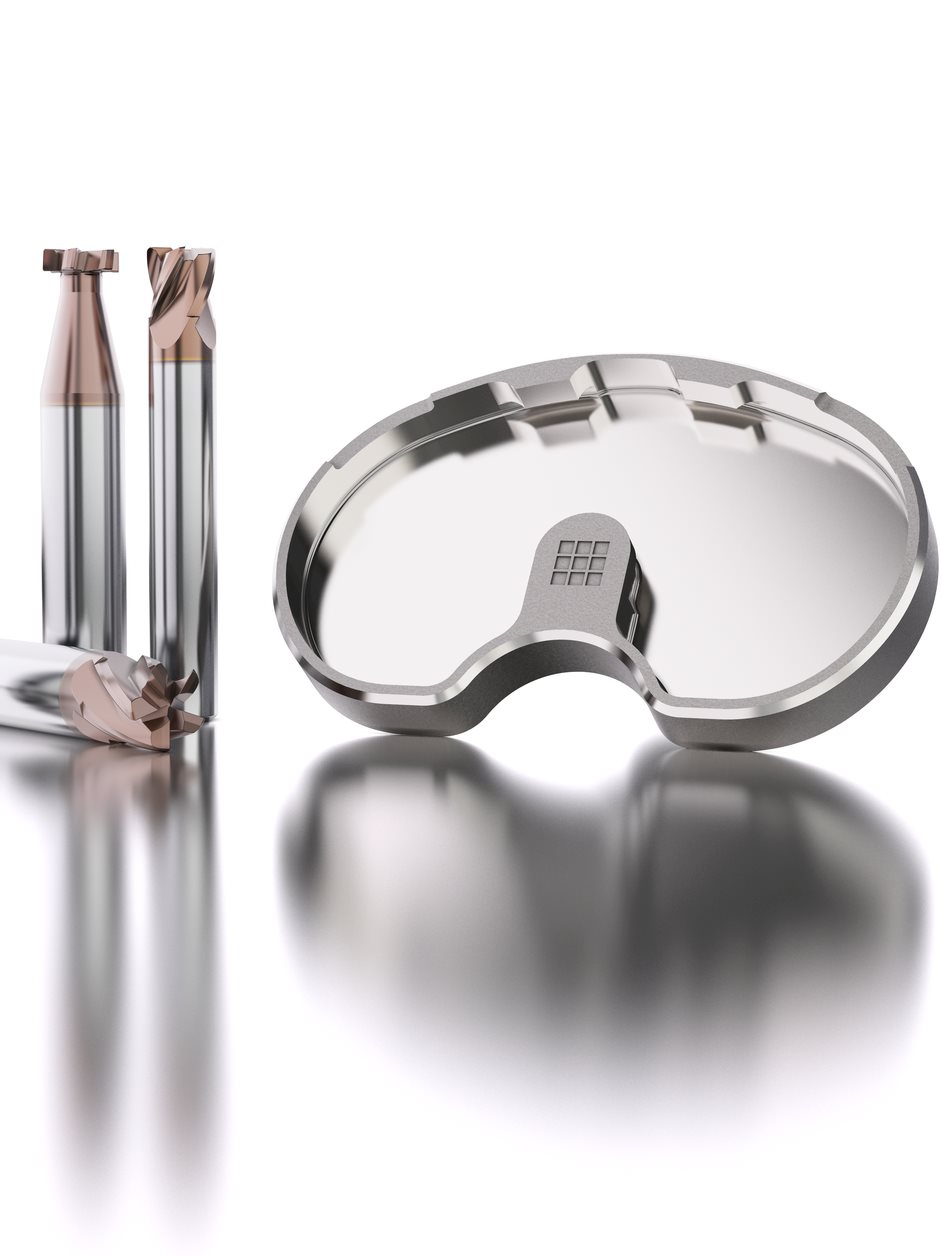
Bearing Inserts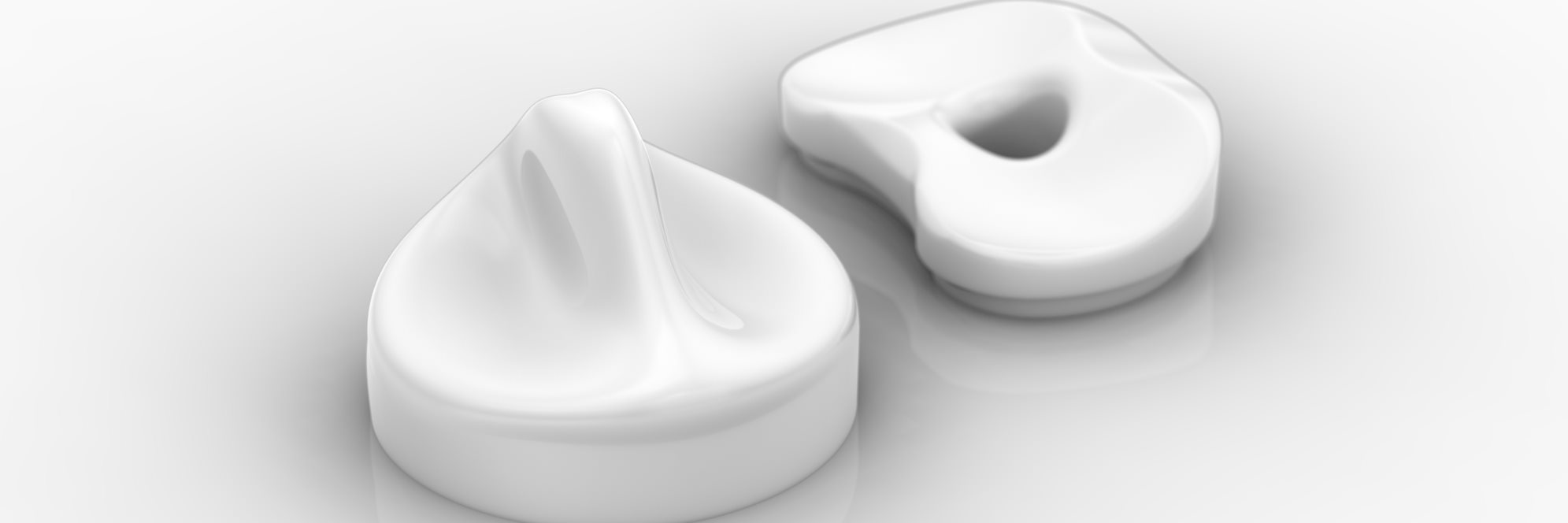
Dental Implant Components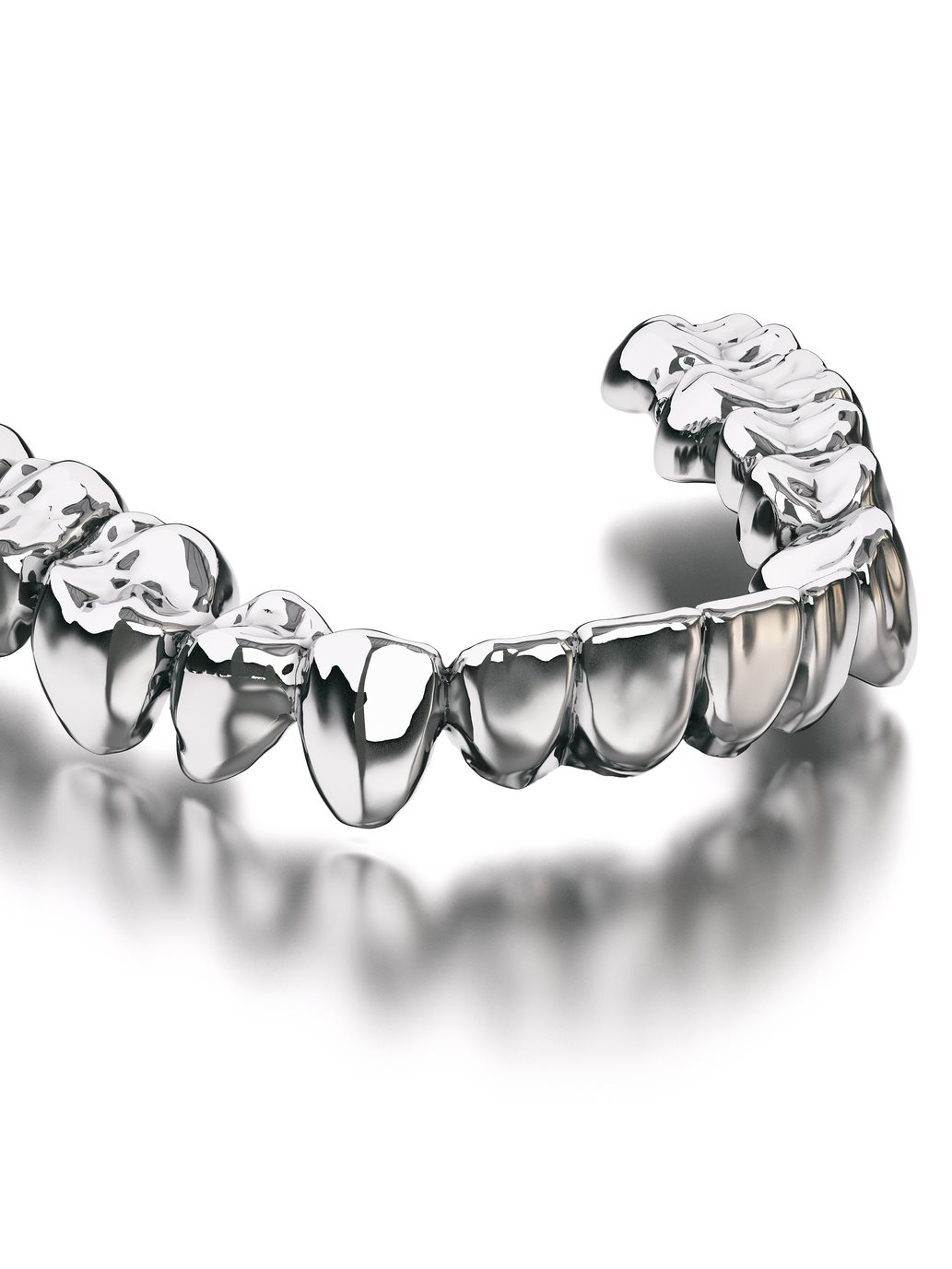
Knee replacement component machining demonstration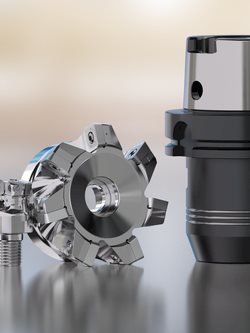
Seco End Mills for Plug-and-Play Dental Milling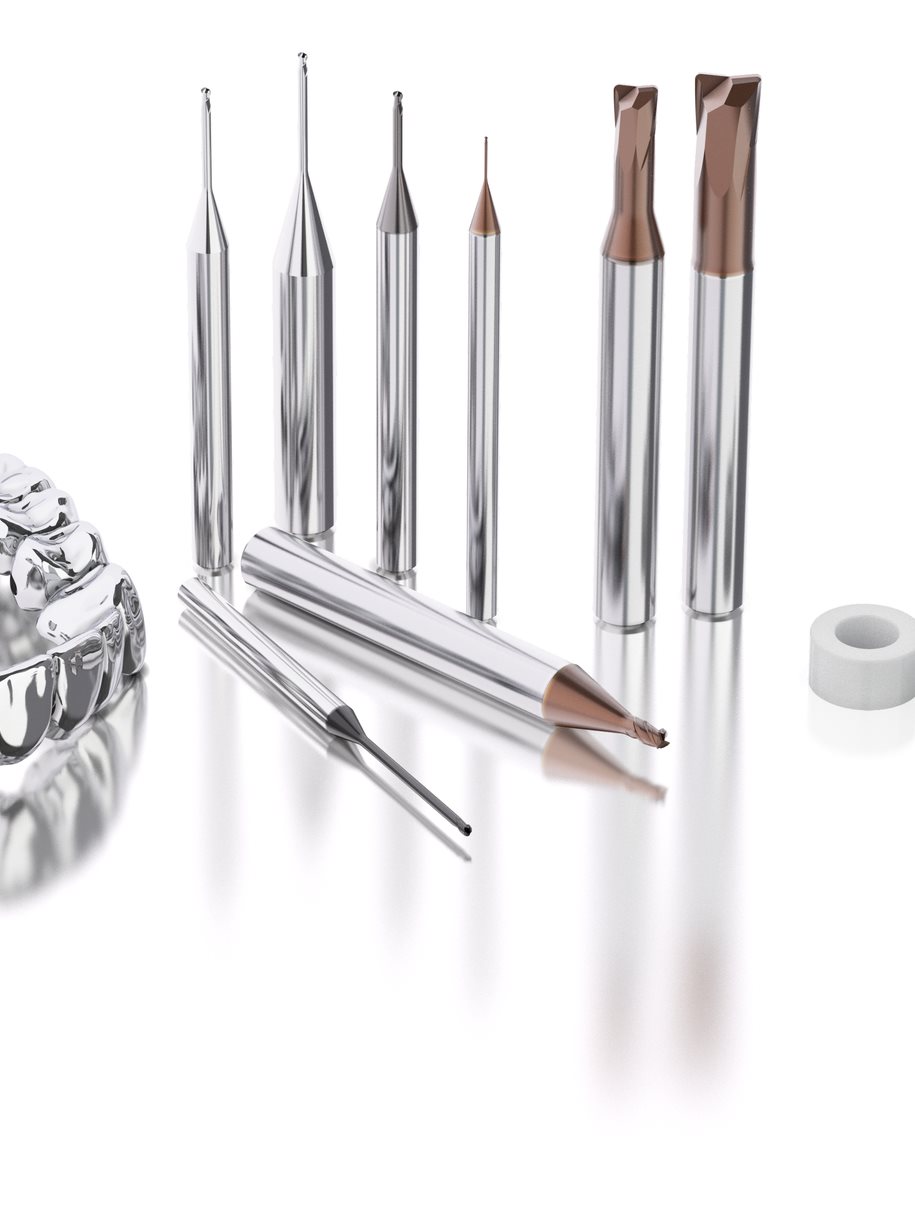
Jabro barrel machining tools - JH734/JH736 & JH744/JH746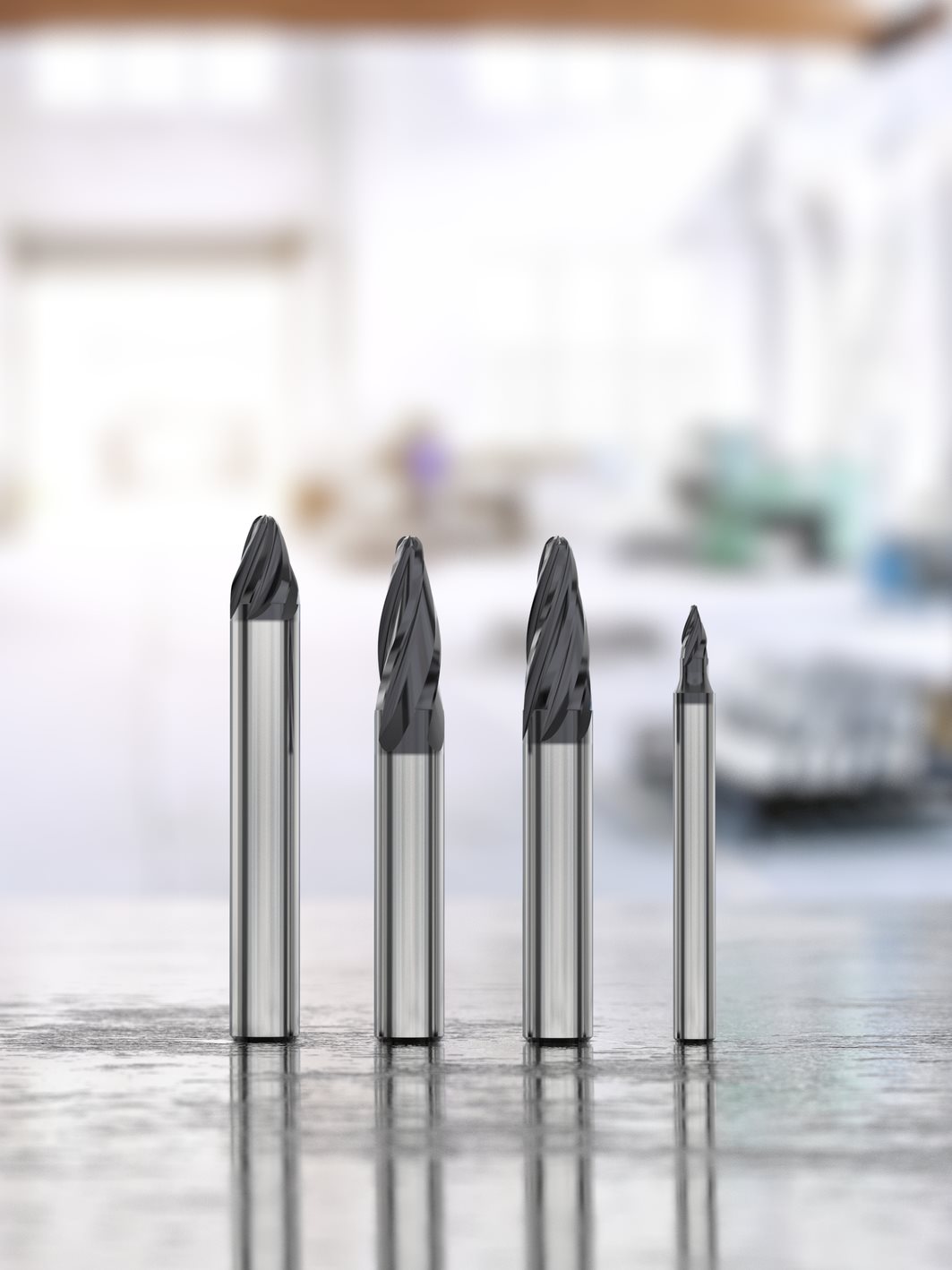
FINISH 3D PARTS FASTER WITH NEW BARREL FINISHING TOOLS DEDICATED TO ISO M AND S MATERIALS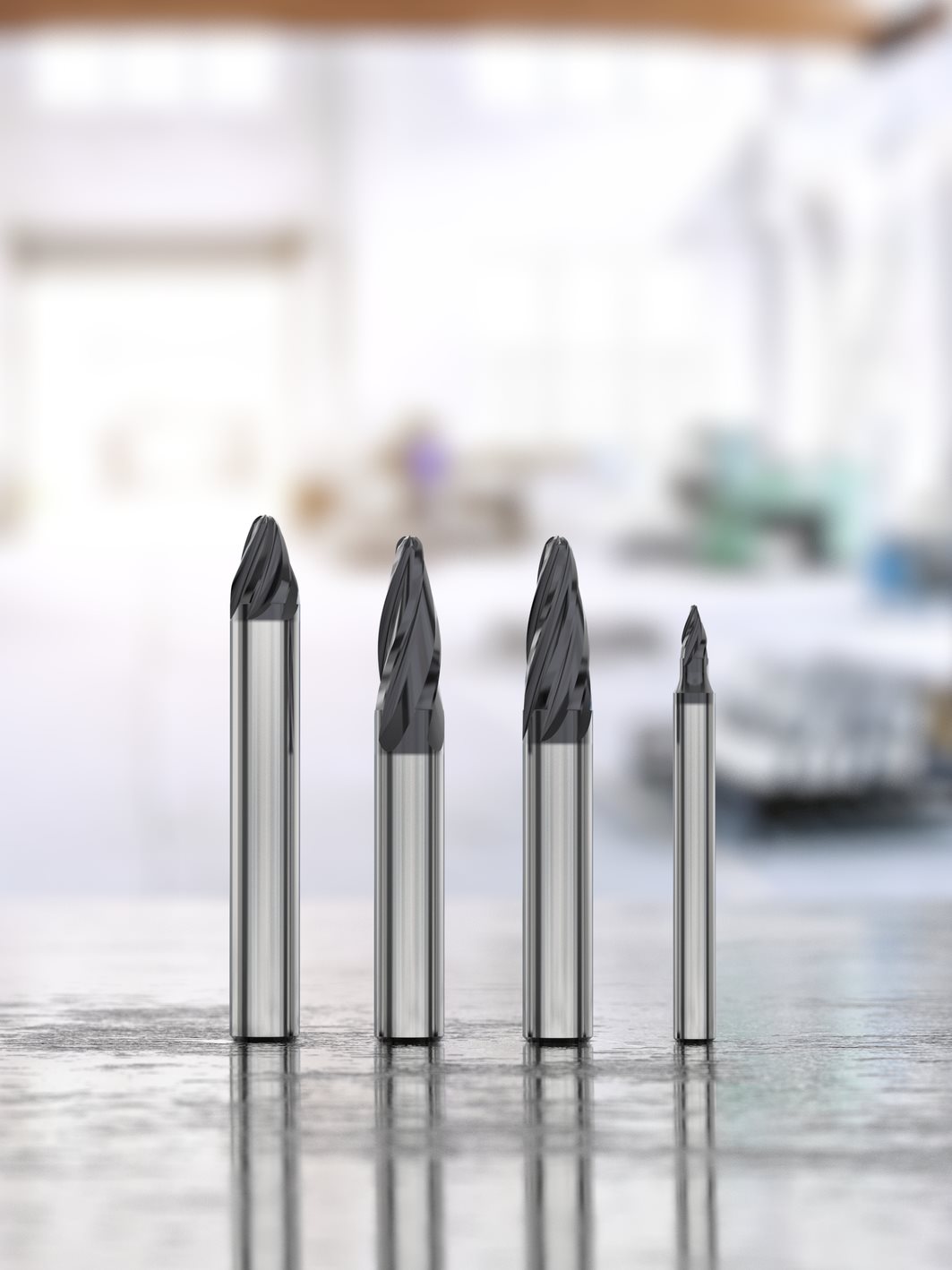
5 Additive Manufacturing Trends Enhancing Production and Tooling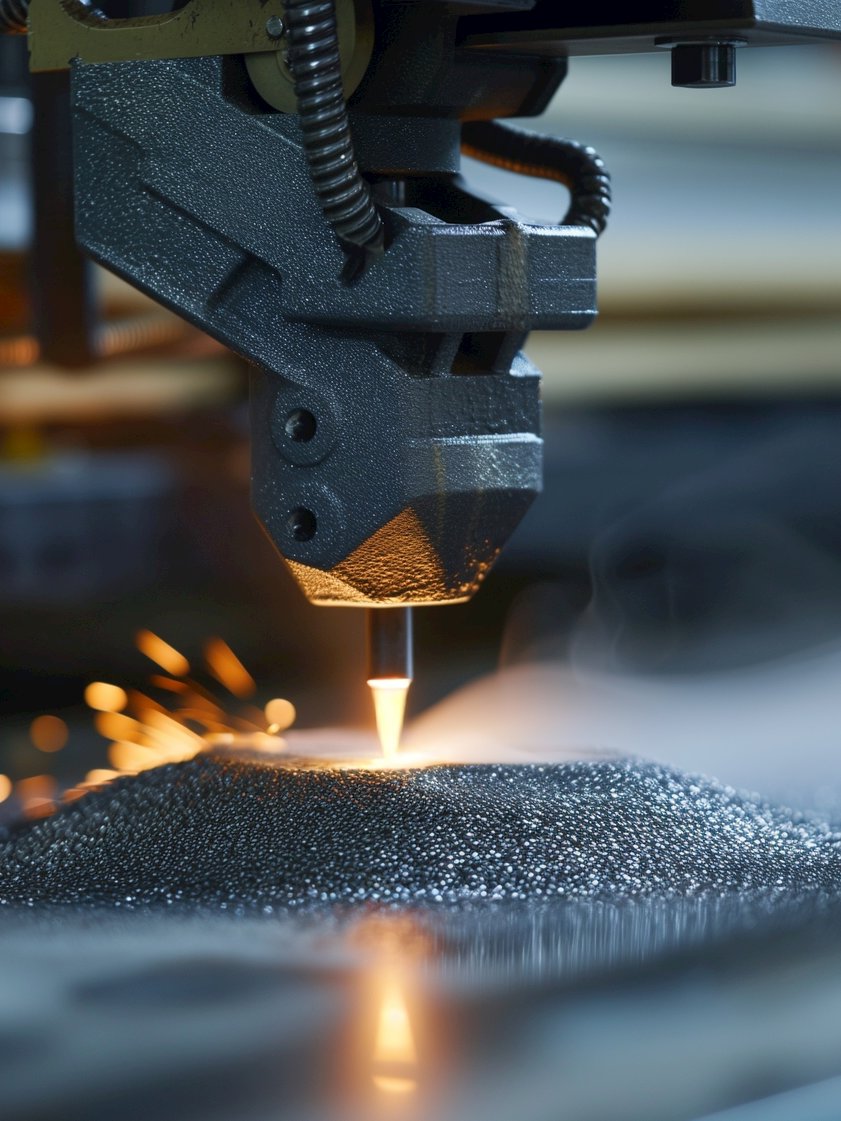
How 3D Printing is Making its Mark in Medical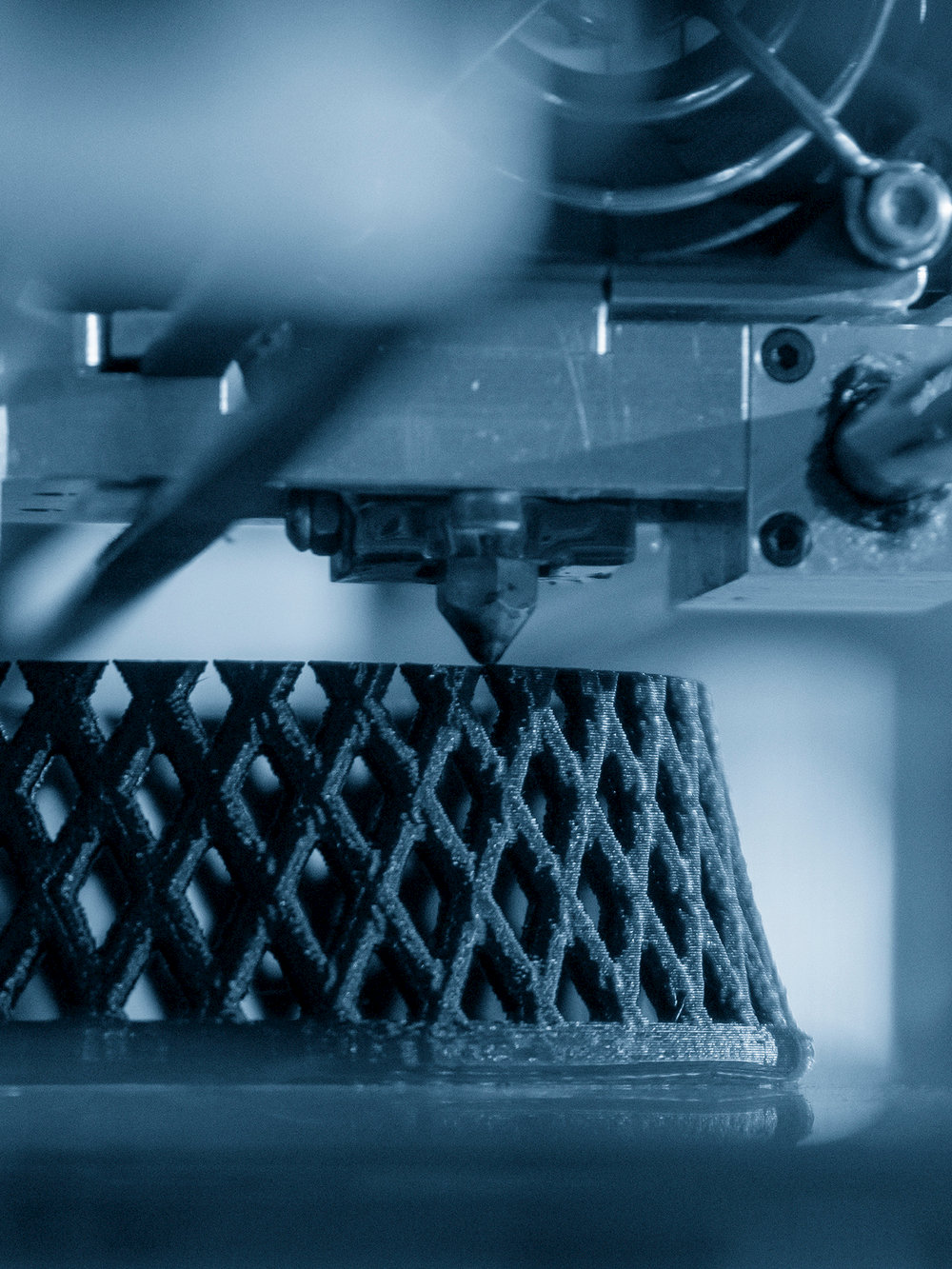
Inspiration Through Innovation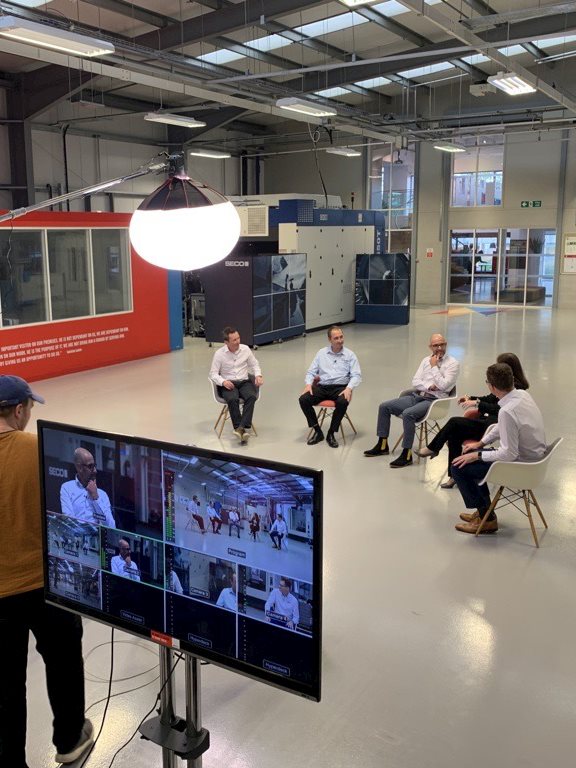
Inspiration Through Innovation 2024: Championing collaboration in the pursuit of manufacturing excellence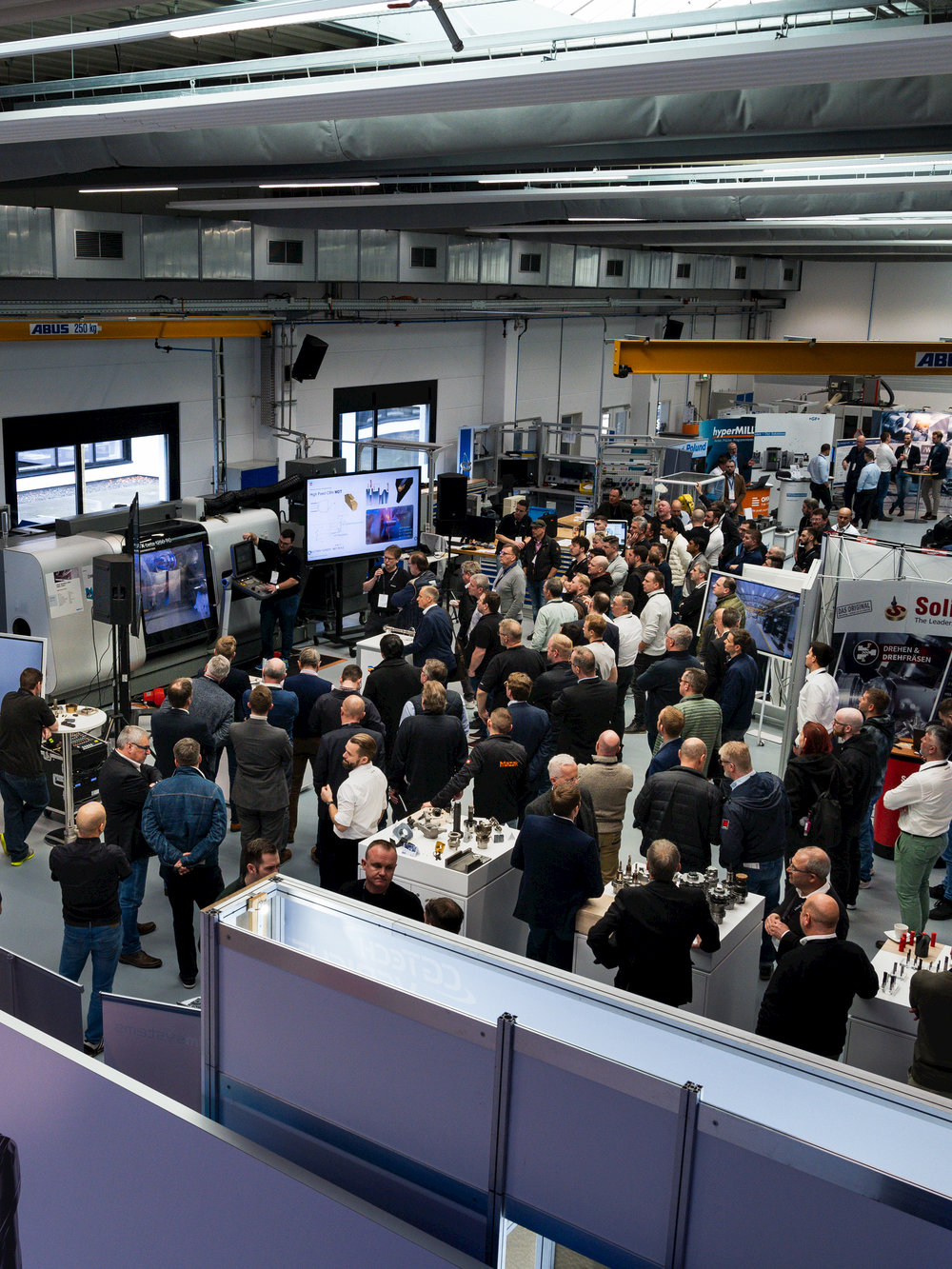
Expert Tips and Insights on Precision Medical Manufacturing | ITI Event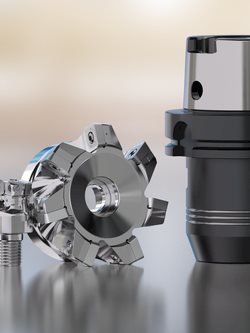
ITI 2024 | Medical Shoulder component machining demo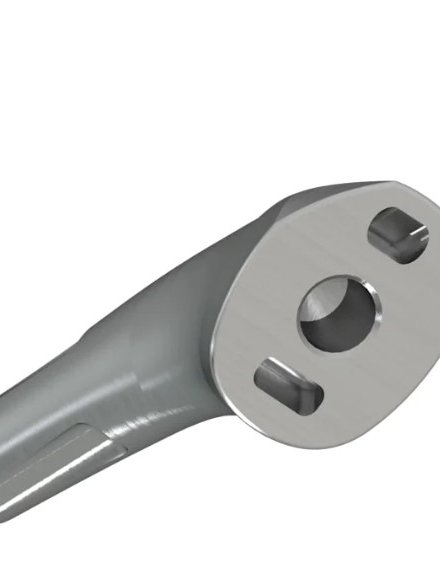
Hip Replacement Components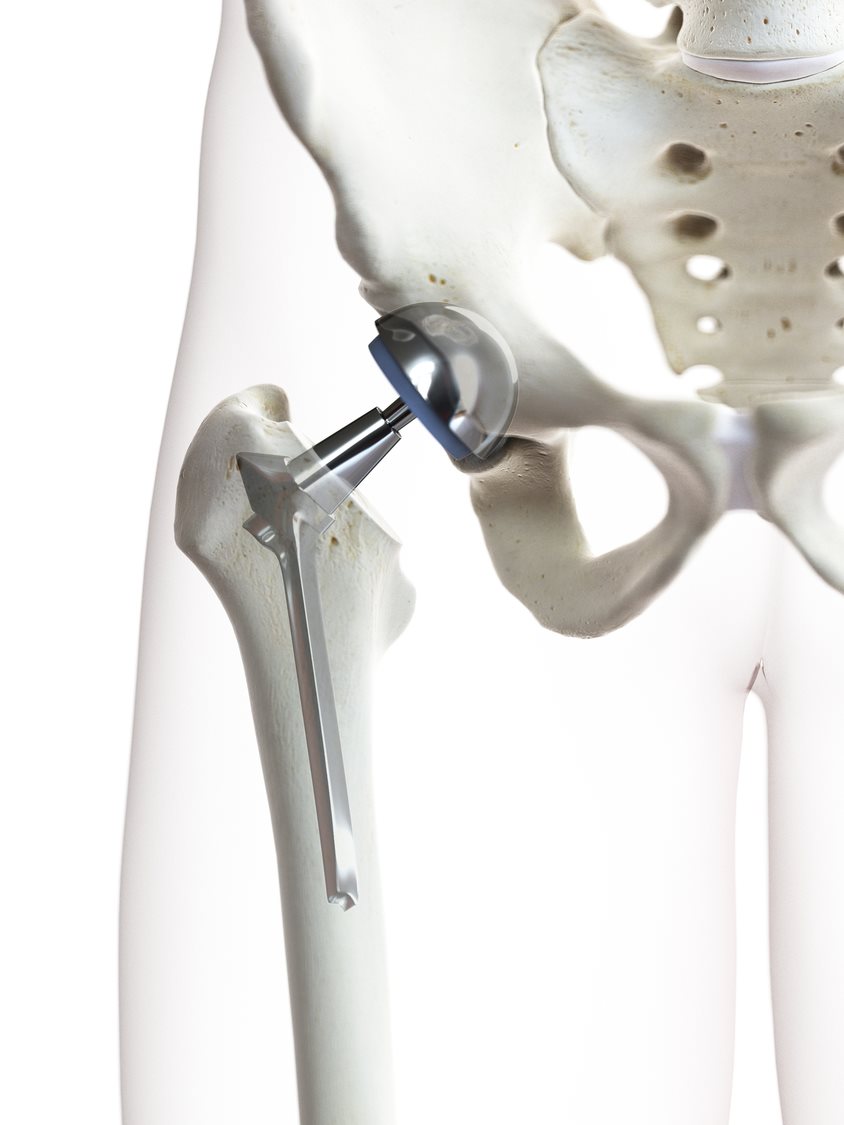
Spinal and Trauma Components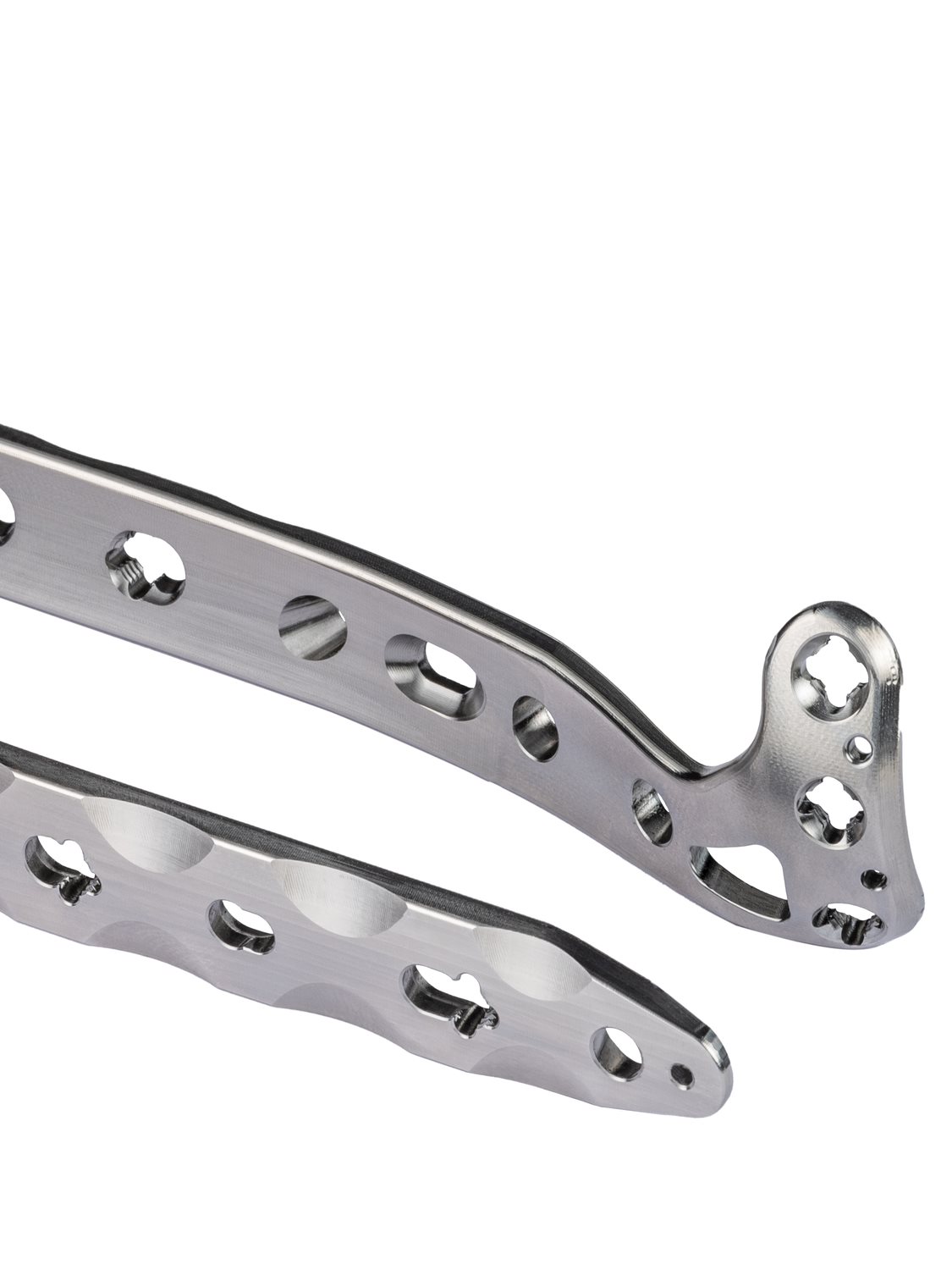
Titanium: Mastering Today’s Challenges, Shaping Tomorrow’s Trends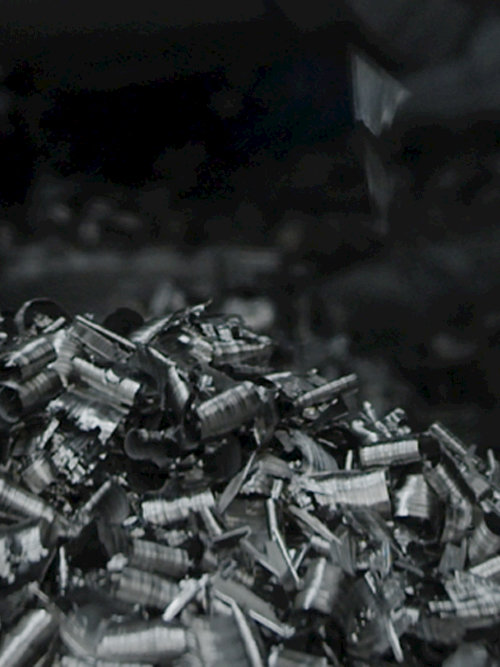
Contact our medical experts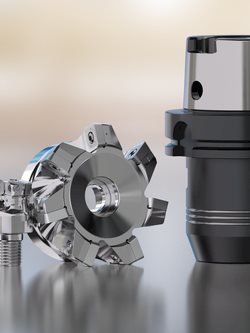
Meet the Mini Mills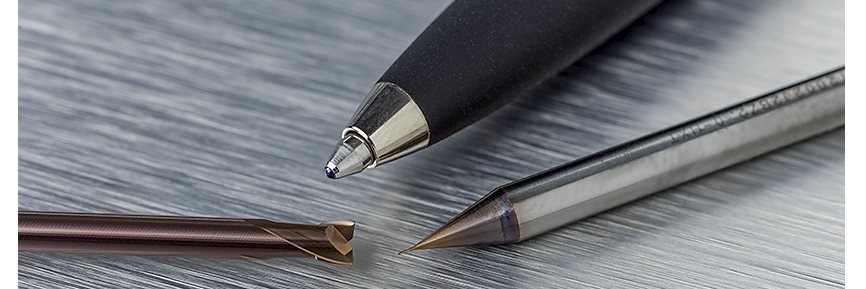
What does it take to engineer for tomorrow?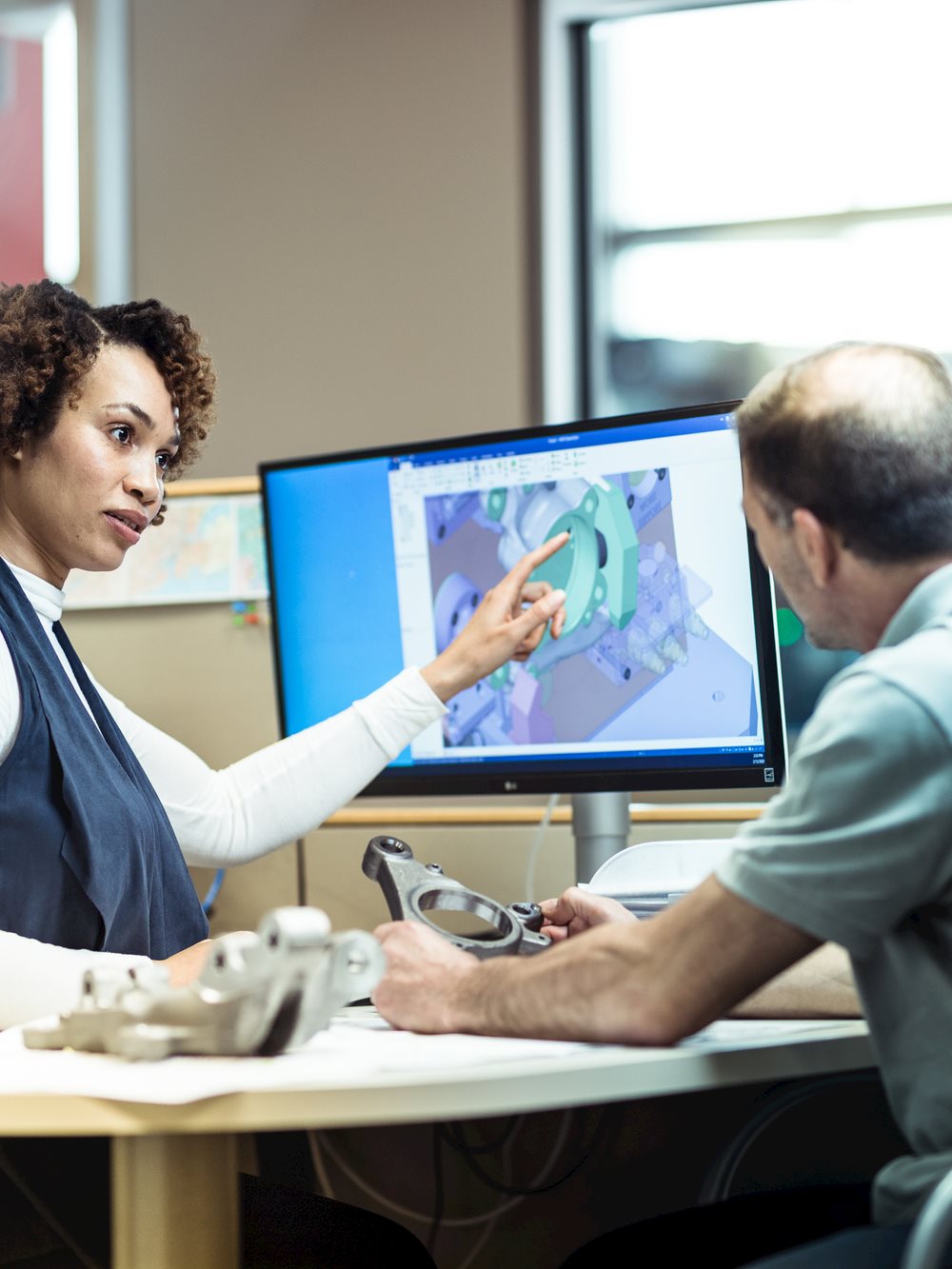
Seco collaborates with GF on machining specific medical components | Seco Tools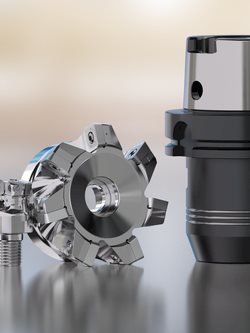
Shank Toolholders and Boring bars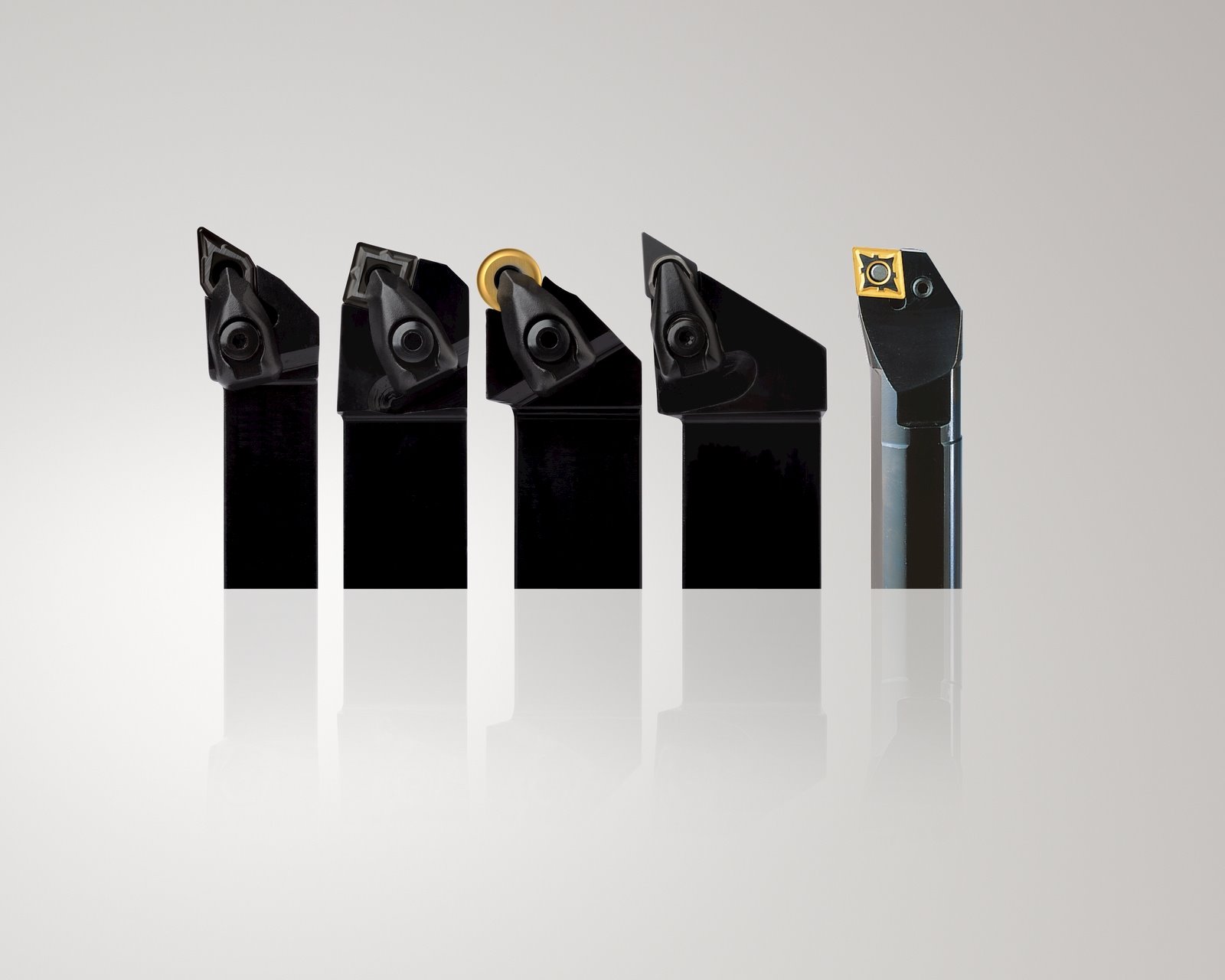
Medical ITI - A Precision medical manufacturing event | Seco Tools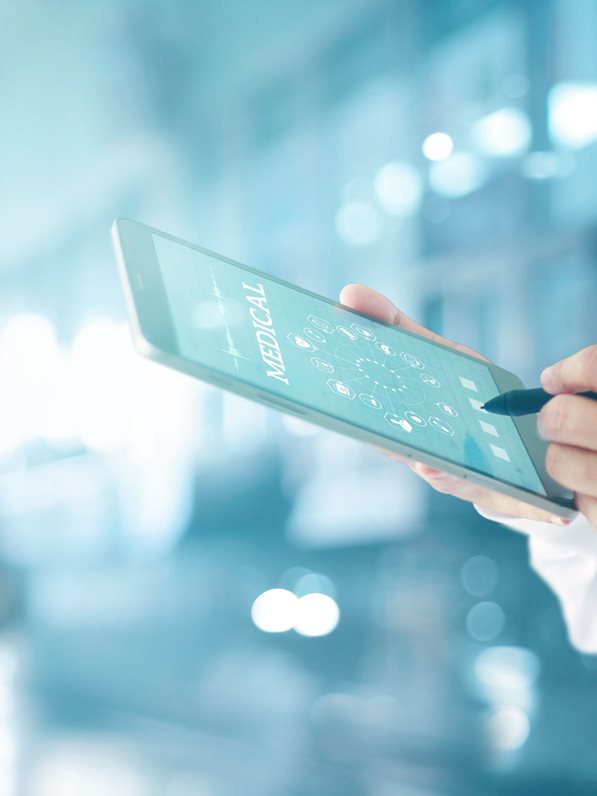
Seco supports Medical innovation with virtual event and exclusive content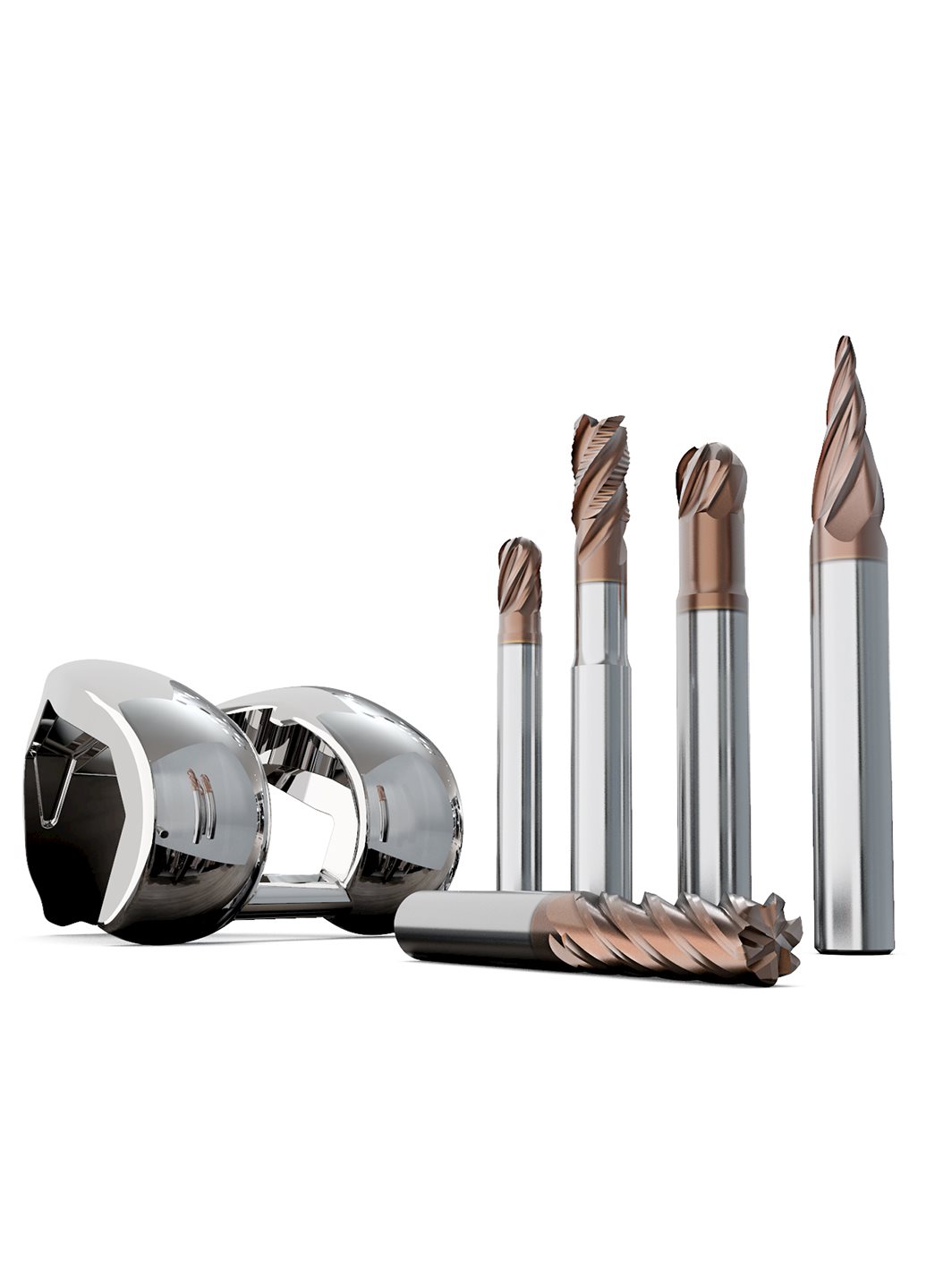
Industries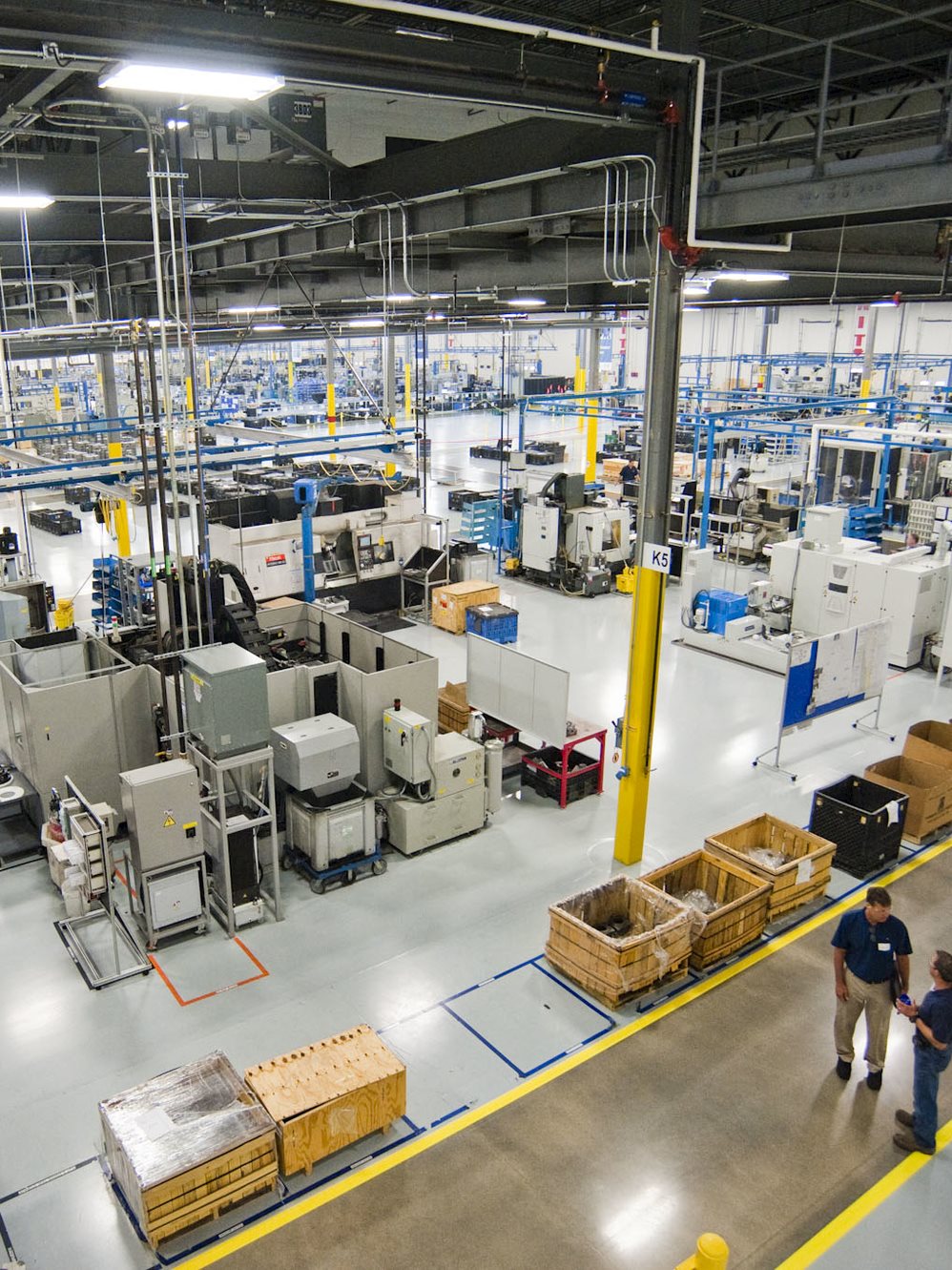
Seco JM500 delivers visible improvements for micromachining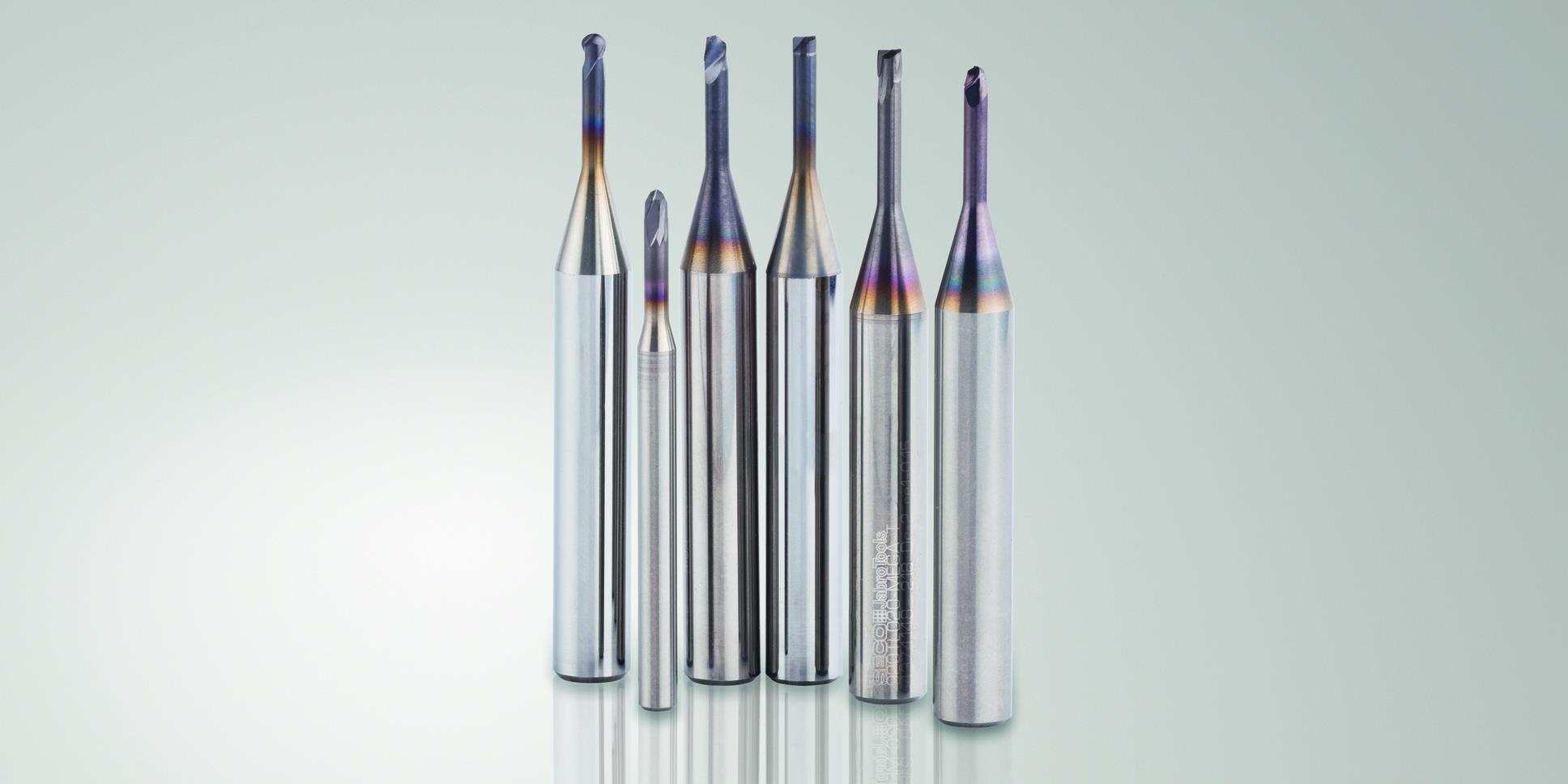
Intelligent future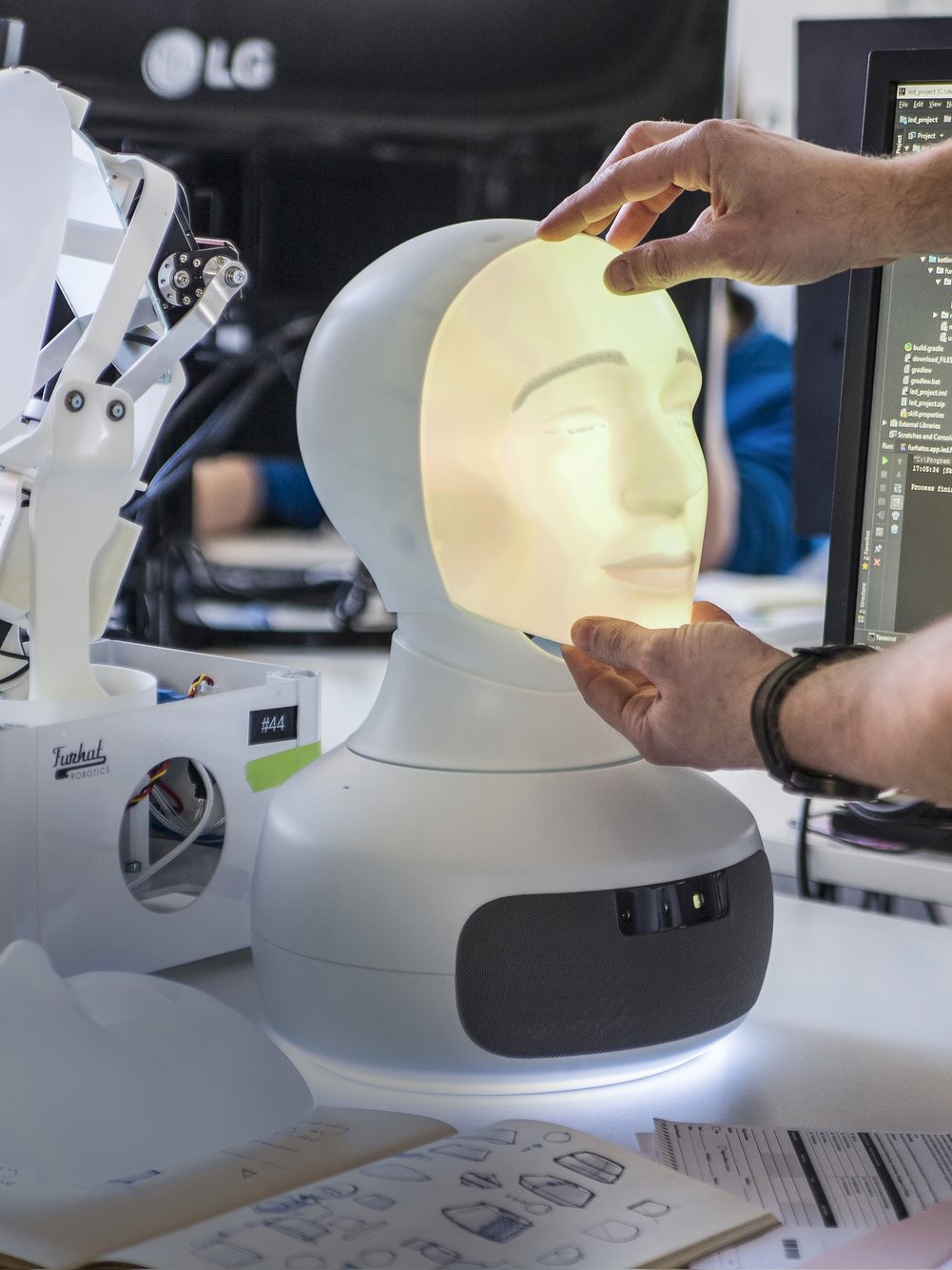
Front-Runners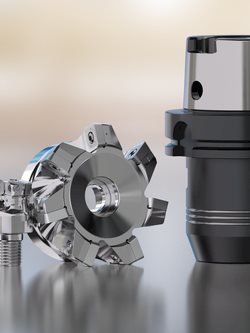
Seco Hydraulic Chucks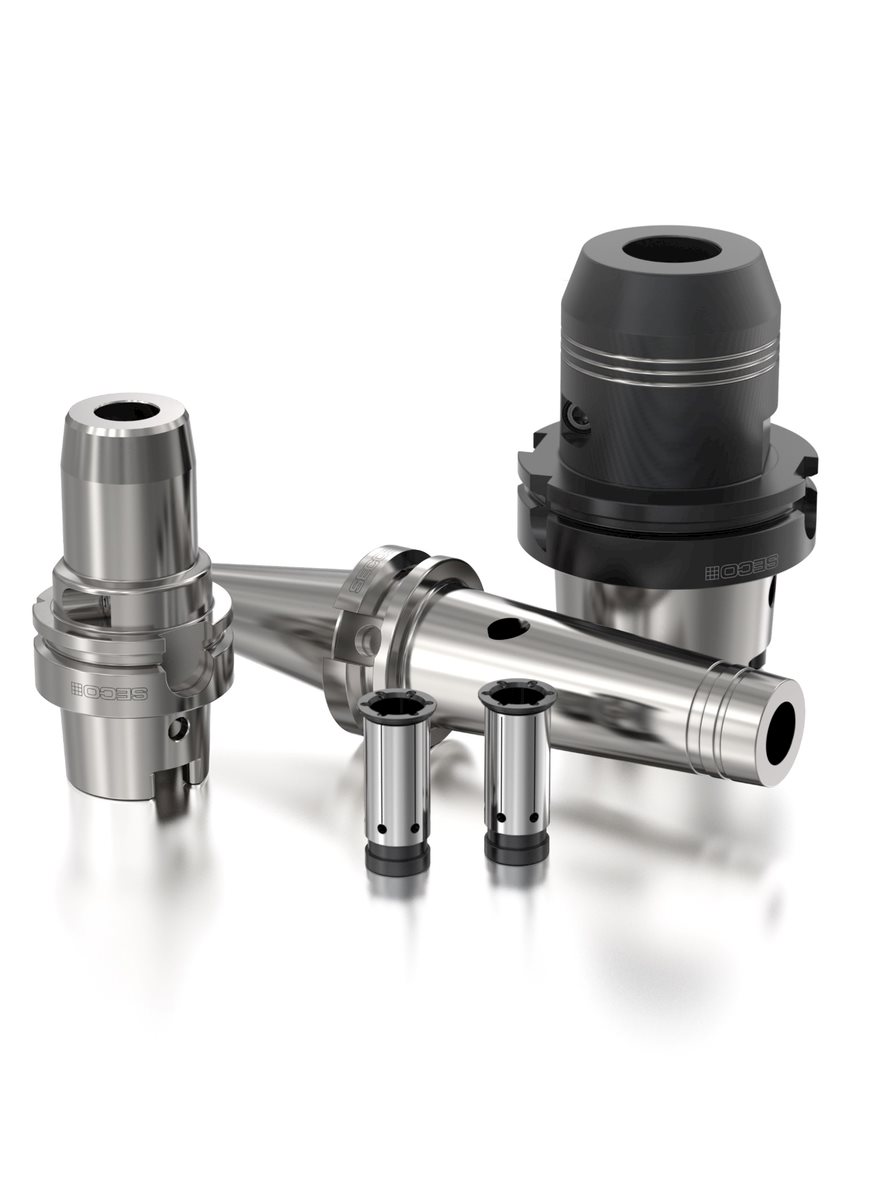
Seco Taps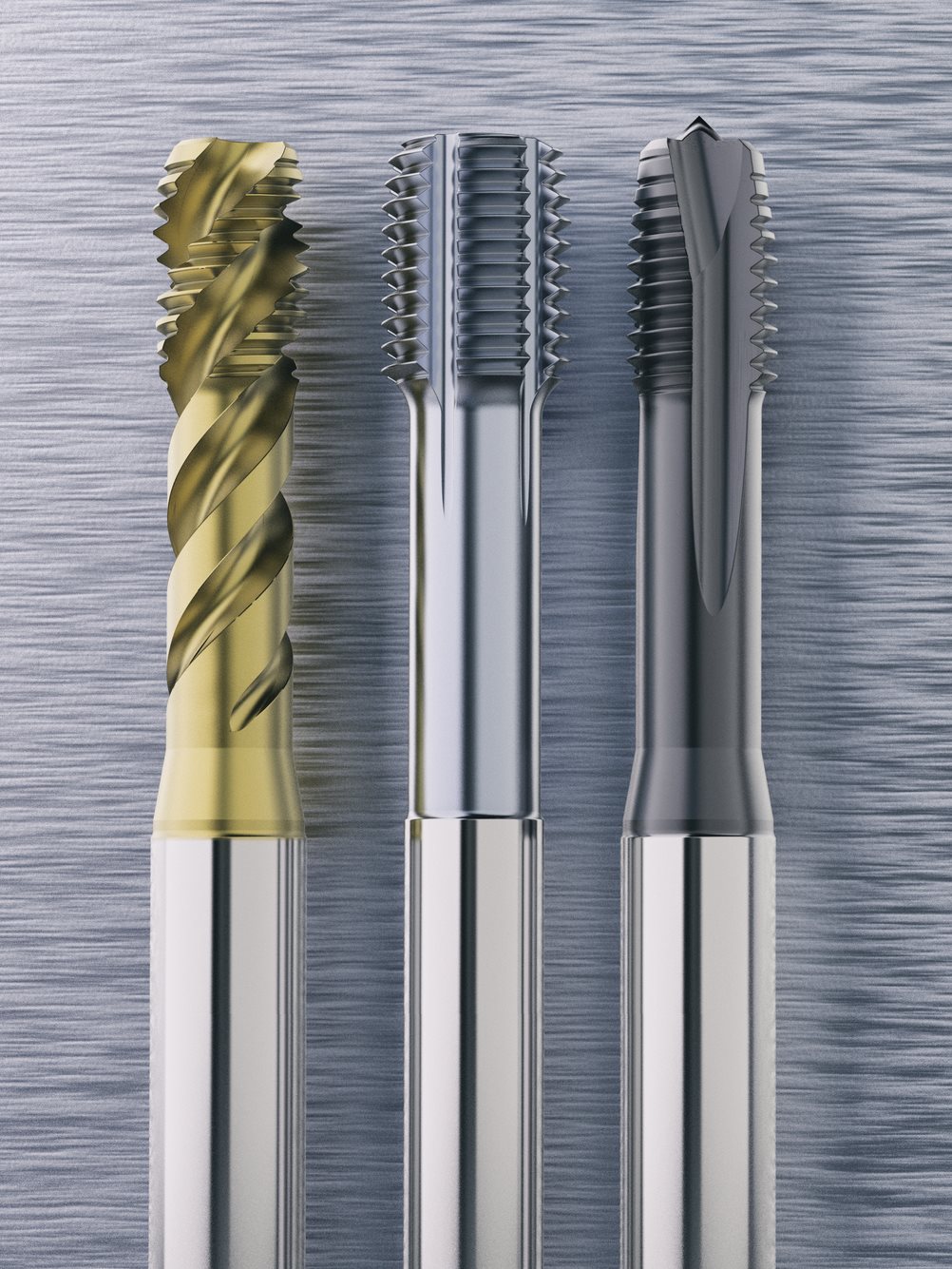
Seco Helical SN8-13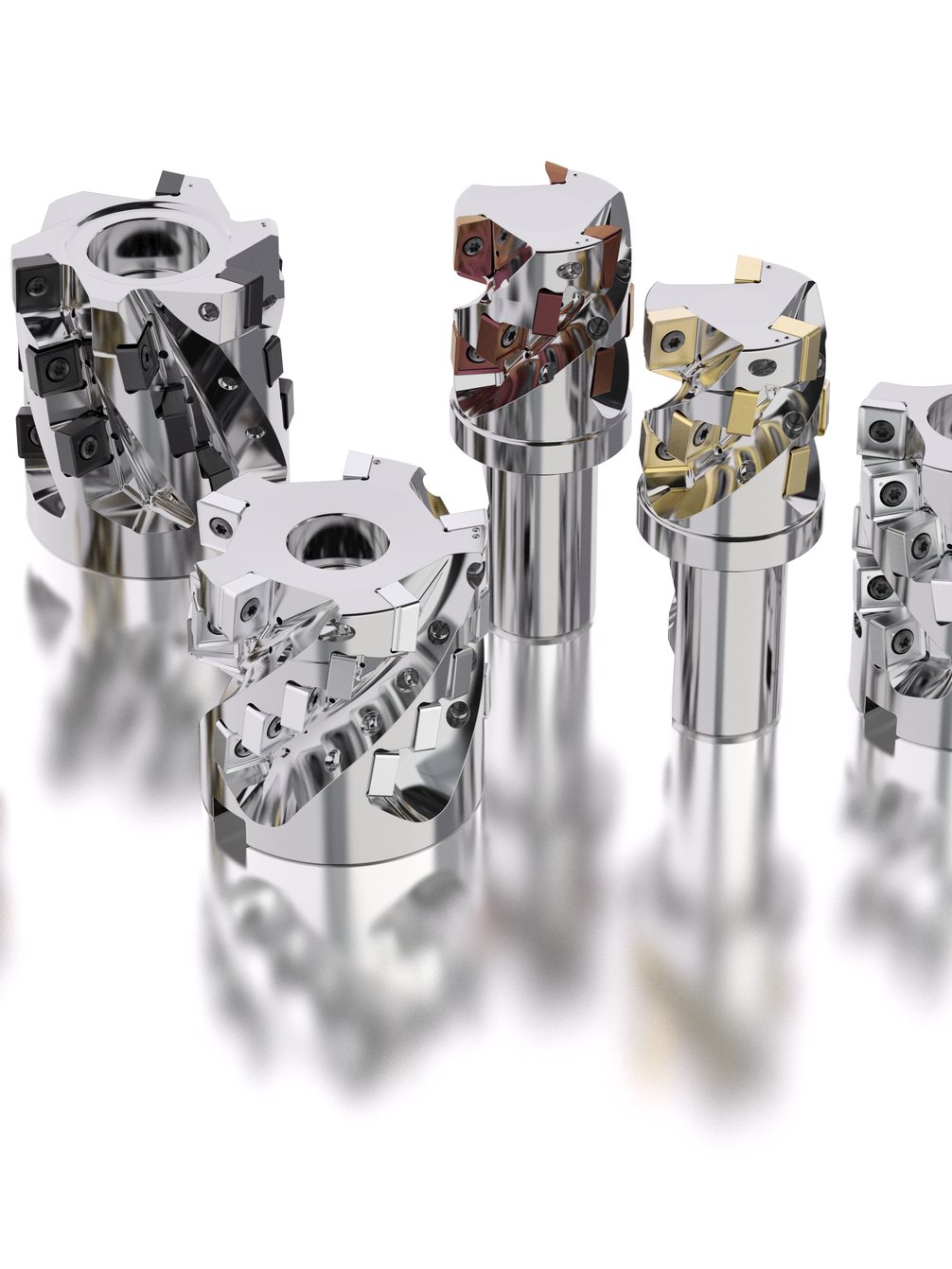
JCO710 - High Performance - Square - Titanium - 4-6 flutes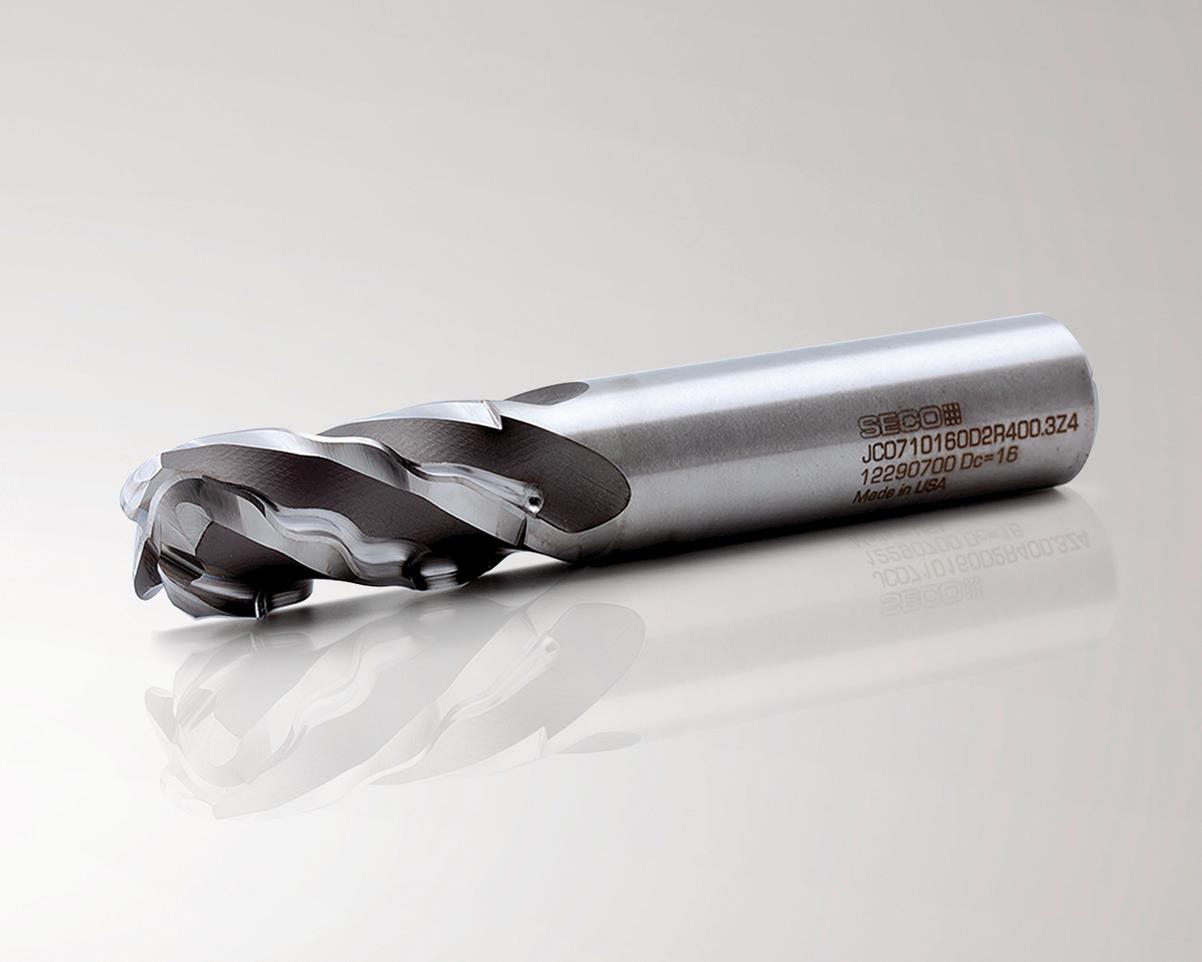
Seco High Feed SP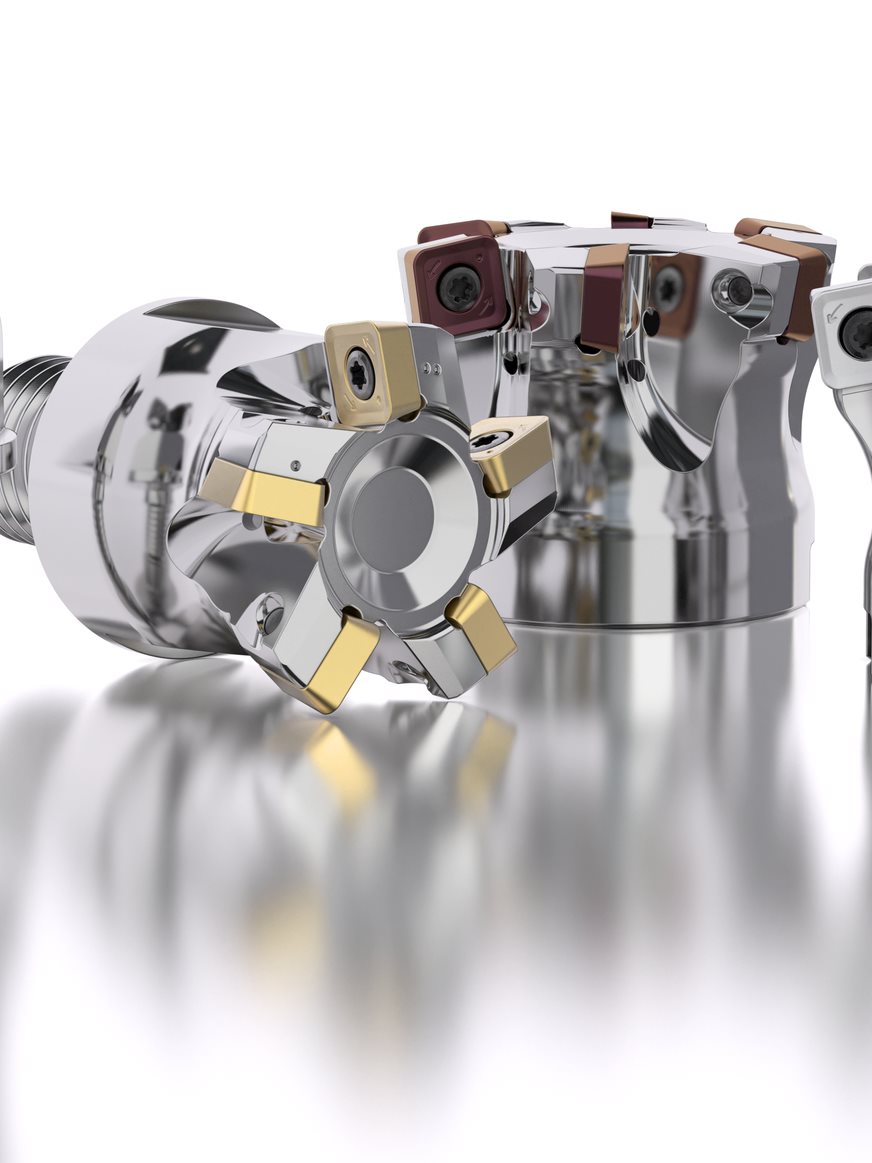
High Performance HSS-Co End Mills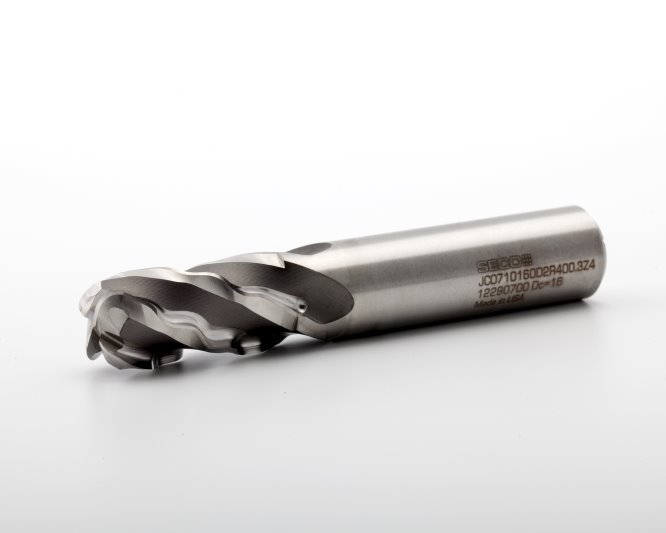
Seco News Summary 2022.2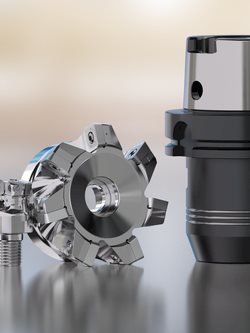
Good news from Cobalt study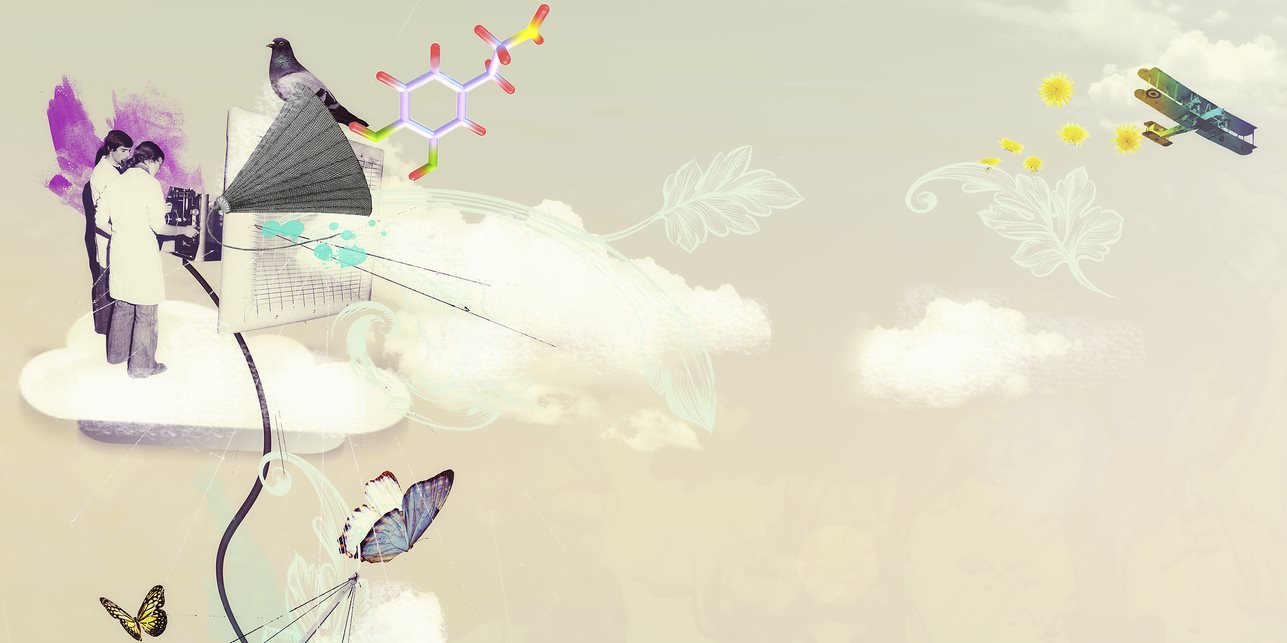
HSS-Co End Mills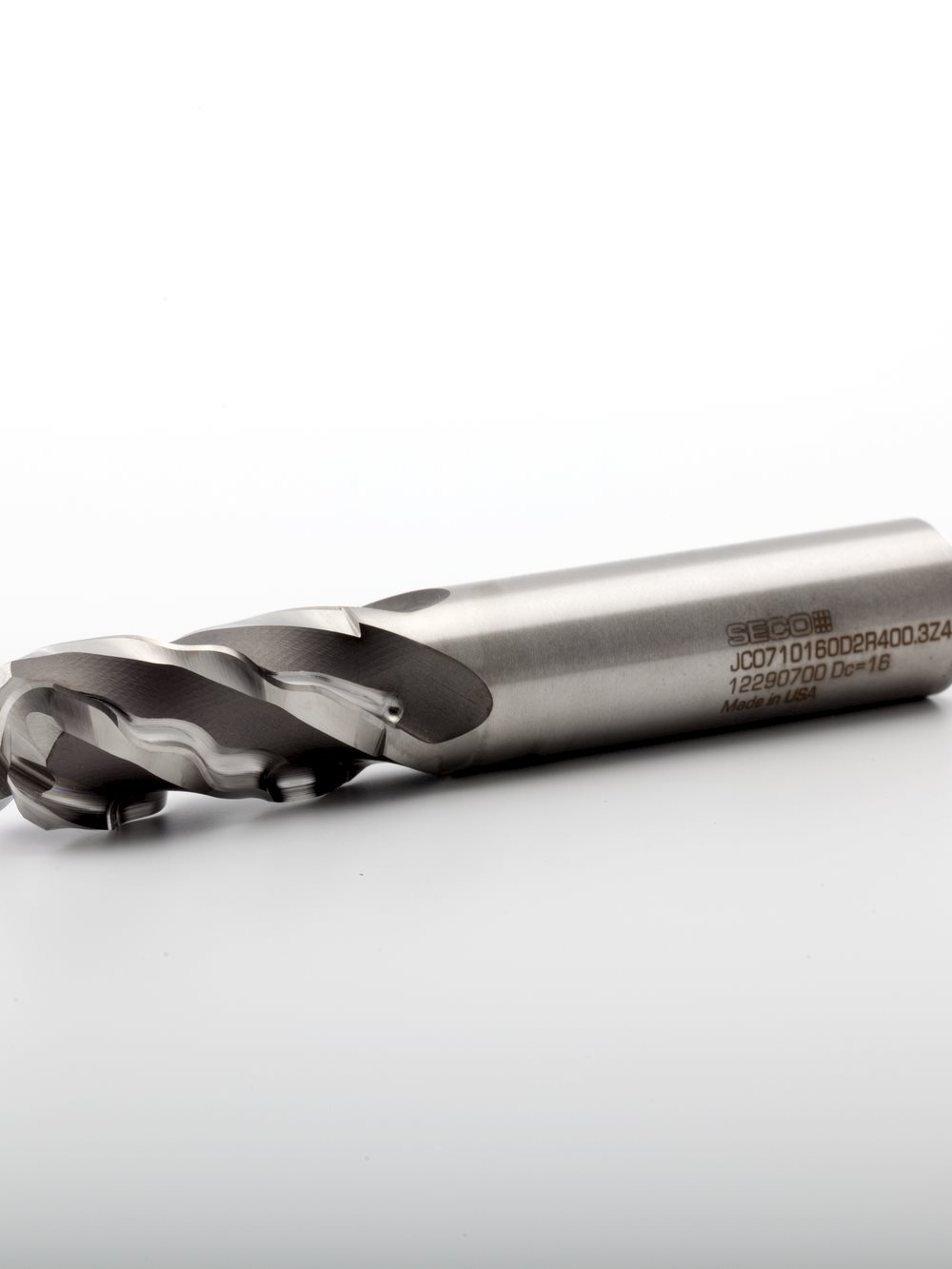
Seco JS754 Stub Series End Mills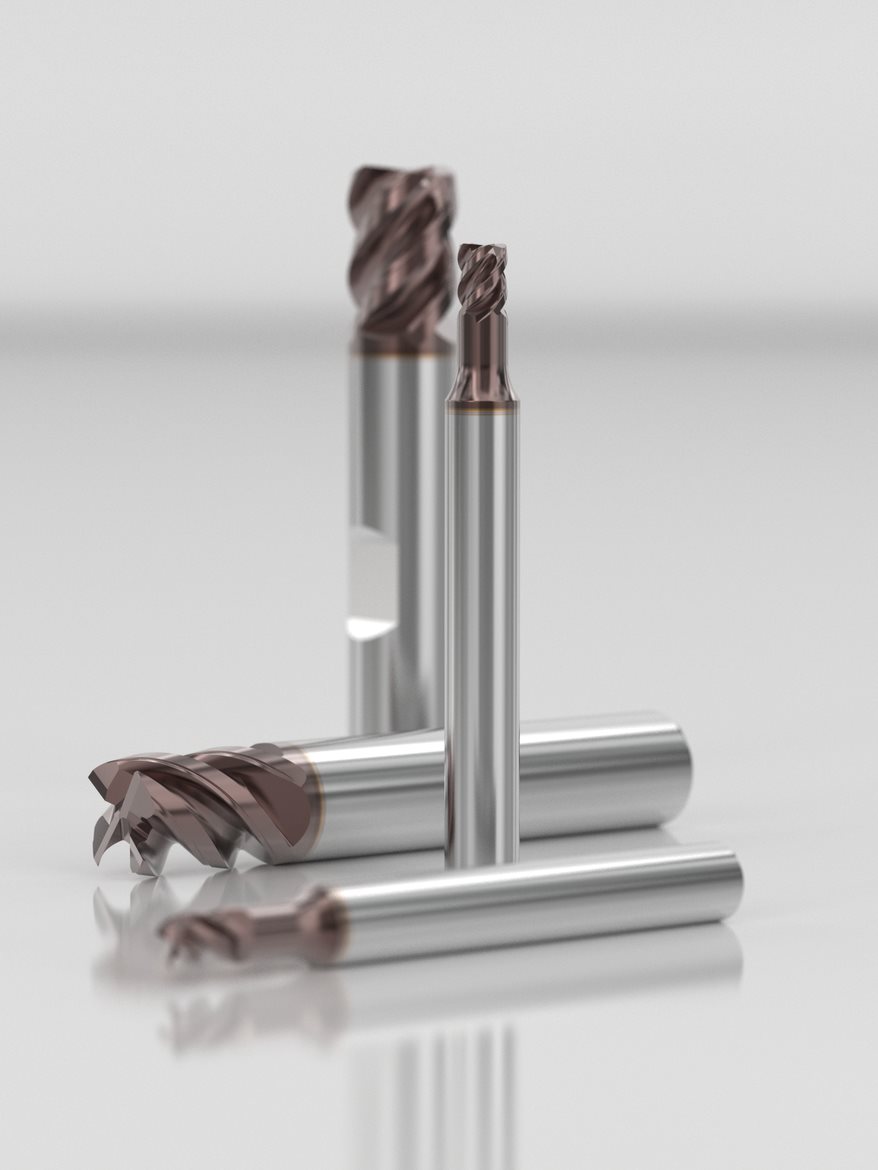
Brochure - Product Highlights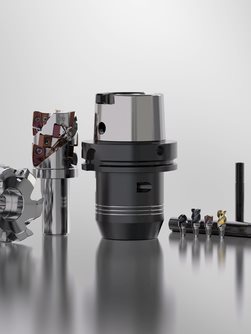
JETSTREAM TOOLING® SECO CAPTO™ GENERAL ISO TURNING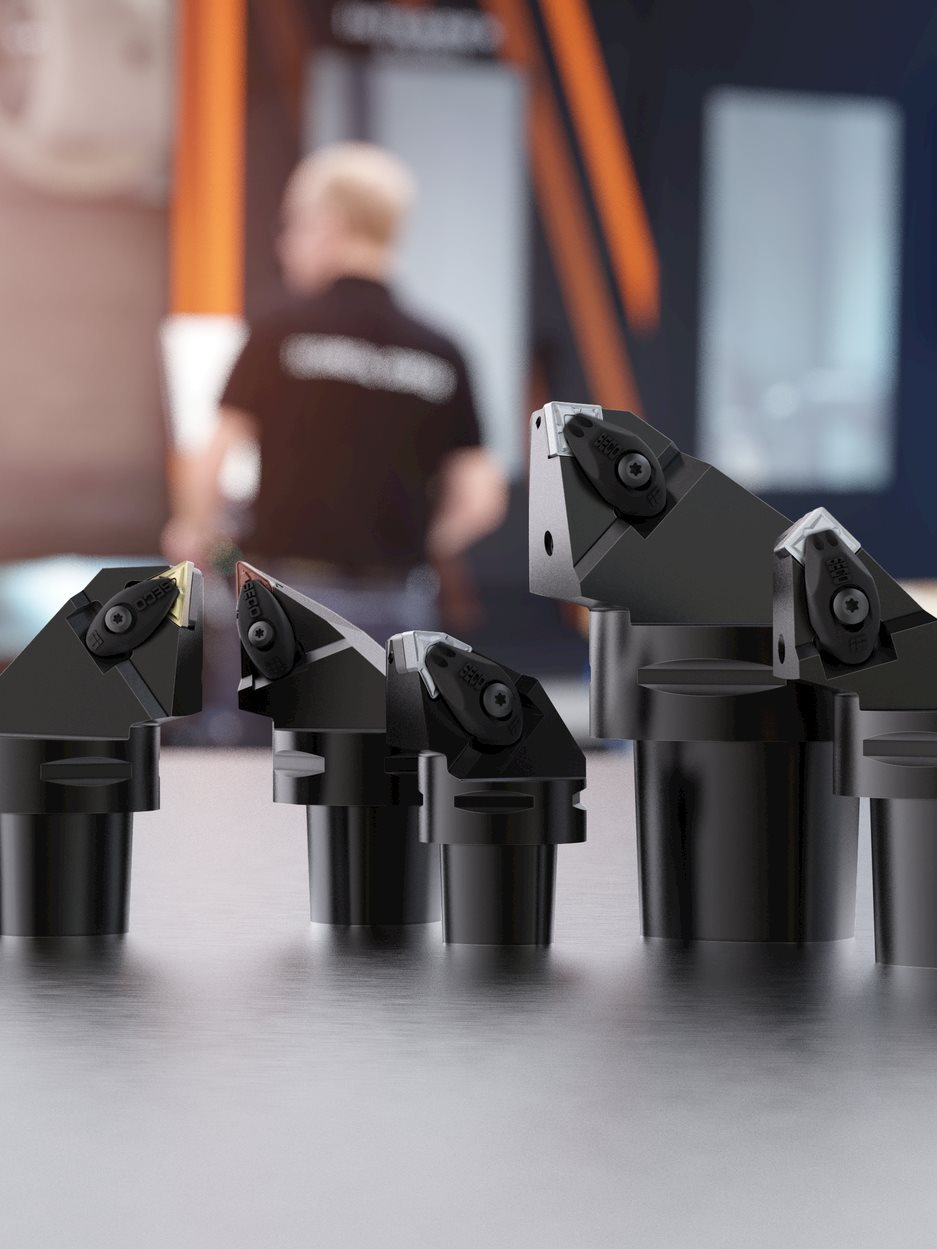