A Powder keg of productivity
With demand for powder metallurgy (PM) components on the rise, PM tooling manufacturer Quala-Die Inc. is always looking for ways to boost output. Seco cutting technology has allowed the company to hard mill and hard turn many tools, increasing productivity.THERE’S A SIMPLE reason why tool and die manufacturer Quala-Die Inc. sits in the heart of Pennsylvania in the United States. The company serves the powdered metallurgy (PM) industry and, as General Manager Richard Schatz explains, the surrounding area creates more PM components than anywhere else in the world.
Quala-Die was founded in 1978 in the basement of the Schatz family’s home and its specialization then, as it is now, was serving the PM compaction sector. Business flourished and the workshop quickly evolved. A new facility was built as the business grew from two to 100 employees, becoming the largest PM compaction tooling supplier in the industry. In October 2016, Quala-Die, Inc. was acquired by another well-known Western Pennsylvania company, Penn United Technologies, Inc. of Cabot and Saxonburg. It has now added to and complemented Penn United’s already broad range of manufacturing service offerings.
The use of power metallurgy components is particularly popular in industries such as automotive, power tools, appliances, RV/ ATV, aerospace, medical and oil & gas. As a result, Quala-Die has continued to experience robust growth and faces a constant challenge to boost capacity and output to keep pace with customer demand. And according to Schatz, the key to overcoming these challenges is always having the most technologically advanced facility and team possible.
“To accomplish that, we have to maintain efficiency and grow in pace with developing technology,” he says. “That means we closely partner with our suppliers to ensure we always have the latest and greatest, whether that is a machine tool, employee training, tooling or even machining strategies – two of which for us lately have been hard milling and hard turning.”
Today’s PM compaction processes are fast, efficient, and extremely accurate, thanks to advancements in powders, dies, tooling and presses. These all allow for the production of components with improved densities and surface finishes as well as nearnet shapes that are closer to final size than was thought possible until very recently.
One of Quala-Die’s customers, for instance, produces PM near-net-shape parts that are within +/- 0.0004" (0.01 mm); and because the parts are so close to finished size they eliminate the need for any secondary finishing processes.
To produce the PM tooling that generates such parts, Quala-Die would typically either grind or electrical discharge machine (EDM) them. But with the latest in cutting tool technology, such as end mills and turning inserts from its tooling partner Seco, the workshop hard mills and hard turns many more of its parts.
Running on high-end machine tools with advanced probing systems, tools from Seco allow the shop to produce parts with tolerances as tight as +/- 0.0001" (0.003 mm), and with extremely fine finishes for closer punchto-die fits, resulting in much more precise PM production parts.
Both hard-milling and hard-turning machining strategies contribute significantly to Quala-Die’s ability to quickly and cost-effectively produce its often complex and high-precision press tooling. Hard machining reduces the amount of finishing processes such as EDM and grinding needed for the tooling and thus shortens overall part turnaround times. Plus, the resulting PM tooling lasts much longer.
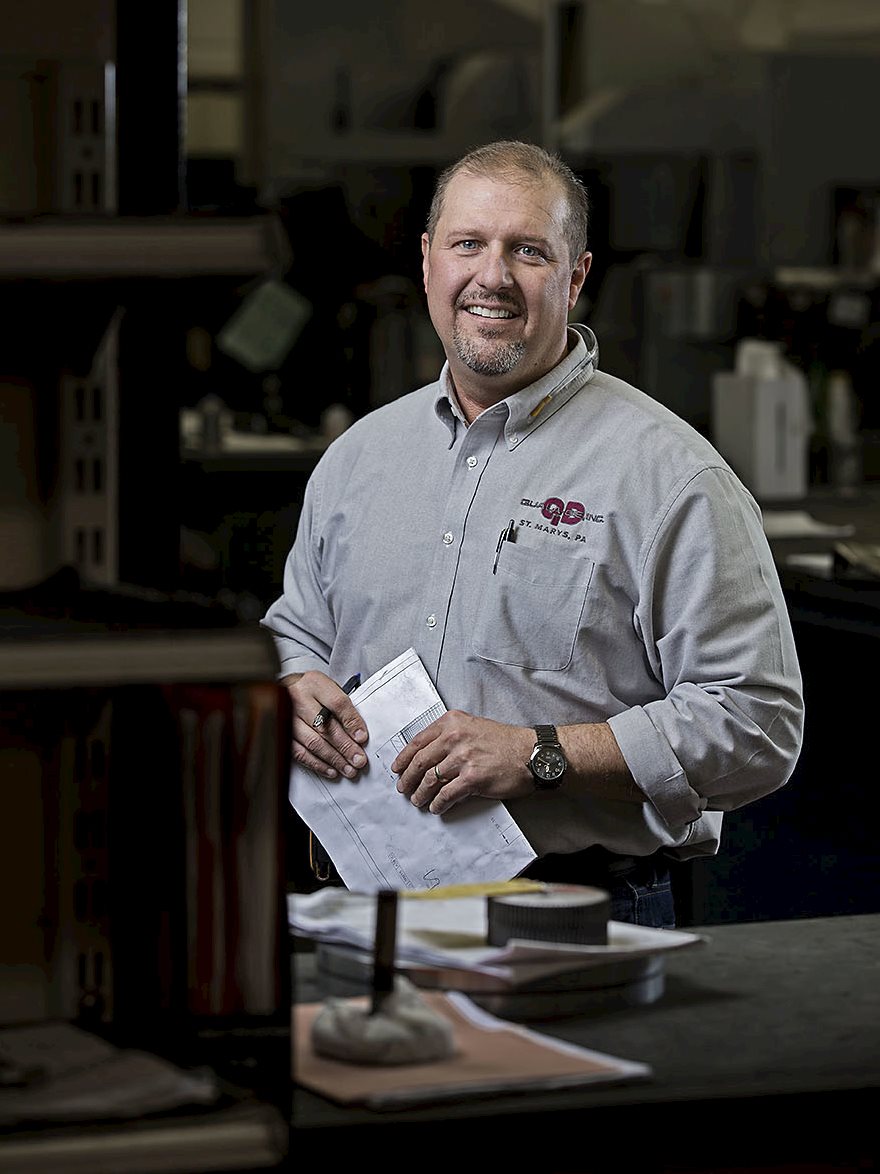
ACCORDING TO SCHATZ, today’s machine tool capabilities allow the shop to take full advantage of Seco’s tooling for hard machining and thus reduce setups and setup times that would be quite costly if the part was processed with EDM or grinding. “We can now produce full tool sets – thanks to hard machining – at a price point that then makes the PM process affordable, so more shops consider the process for their components,” he says.
Quala-Die has worked with Seco for over 35 years. One of the many significant contributions Seco has made was when the tooling company suggested Quala-Die use hard milling techniques and Seco’s line of solid carbide end mills. Following up on that success, Quala-Die employed Seco’s Niagara Cutter diamond coated carbide end mills for milling abrasive graphite EDM electrodes.
TODAY, QUALA-DIE employs a wide variety of Seco solid end mills to easily and confidently mill tool steel components as hard as 60–65 HRC. These steels have relatively high amounts of vanadium and chromium, making them as hard as traditional high-speed steel (HSS) end mills. That fact makes HSS tools impractical. As a result, many metal working companies believe the only way to produce these hard parts is to use grinding operations. But this is no longer the case thanks to advancements in flute design and helix angles, along with substrate and coating structures.
For its hard turning, Quala-Die uses TH1500 and CBN200 Seco insert grades and eliminates having to cylindrical grind part IDs and ODs. The TH1500 grade’s profile includes a textured α-based Al2O3 CVD coating, Ti (C,N) middle layer and a superfine grain substrate that make the grade well suited for machining hardened steel workpieces.
Schatz adds that Quala-Die sees a lot of growth potential not only in the PM indus - try but also in diversification. The shop would like to expand into other industries, such as the rotary die industry, and do more prototyping and production jobs, especially where connecting rods are concerned. Quala-Die plans to continue to invest in equipment and human resources, as well as optimize its machining capabilities. And for that, Schatz says the shop will rely on Seco.