MEP は航空機製造産業の最先端に位置する
製造企業は、加工製品を製造するために旋削加工、フライス加工、ドリル加工などを活用しています。ただし、これらの加工プロセスにより、加工製品の境界部にバリや鋭いエッジが形成される可能性があります。これらの鋭利なエッジ状態は、加工製品の製造中に被削材の欠損を引発生させて、構造的に脆弱化し、作業オペレータに危険をもたらす可能性があります。このような負の条件が、多くのエンドユーザーが、サプライヤから部品を拒否する理由としてバリや非常に鋭いエッジを考慮する理由です。製造企業は、加工製品を製造するために旋削加工、フライス加工、ドリル加工などを活用しています。ただし、これらの加工プロセスにより、加工製品の境界部にバリや鋭いエッジが形成される可能性があります。これらの鋭利なエッジ状態は、加工製品の製造中に被削材の欠損を引発生させて、構造的に脆弱化し、作業オペレータに危険をもたらす可能性があります。このような負の条件が、多くのエンドユーザーが、サプライヤから部品を拒否する理由としてバリや非常に鋭いエッジを考慮する理由です。
製造企業は従来から、ハンドグラインダーや手作業によって、バリや鋭利なエッジを除去してきました。このような方法では時間がかかり、バリ取りや面取り作業のために加工製品を工作機械から取り出し、再セッティングする必要があります。また、熟練オペレータがこれらの作業を行ったとしても、加工製品ごとに必要な加工プロセスの均一性を維持できません。
手動バリ取り作業に代わる生産的な代替手段は、機械化エッジプロファイリング (MEP) です。MEP は、加工製品を製造するのと同じ機械設備とエンジニアリングツールを適用することで、切除が必要なエッジ状態を加工除去します。MEP 加工プロセスには多くの利点があります。これにより、機械設備の CAM システムを通じて最終的なエッジ状態を正確に定義およびプログラムできるため、製品形状の均一再現性が最大限に高まります。加工製品を機械設備から取り外して再セッティングする必要が無くなるため、公差精度の累積誤差やその他の均一性不整合が解消されて加工品質が向上し、全体的な生産プロセス時間が短縮されます。 この傾向に対応して、今日の切削工具メーカは、MEP プロセスの利点を強化する、革新的で生産的な工具の開発を続けています。
航空機製造産業では、加工製品の精度と品質均一性の要求水準がますます厳しくなっており、ジェット航空機の構造部品は MEP に最適の対象製品です。
たとえば、航空機のタービンエンジン部品は、一般に非回転部品と回転部品に分類されます。ドラムやケーシングなどの非回転エンジン部品の MEP の場合、エッジプロファイリングは通常、加工製品を製造する機械設備に適用される標準的な面取りツールおよびエッジ切除ツールで処理されます。
タービンファンやコンプレッサーディスクなどの重要な回転部品については、製造企業は非常に厳しい製品基準を持っており、加工製品の欠陥を完全に除去することを要求しています。通常ではエッジ状態は、ラボでの承認と認証を受ける必要があります。これらの加工製品のバリを除去するために、切削工具メーカは高精度で完全に均一加工精度を維持できる、カスタム MEP 工具を開発しました。
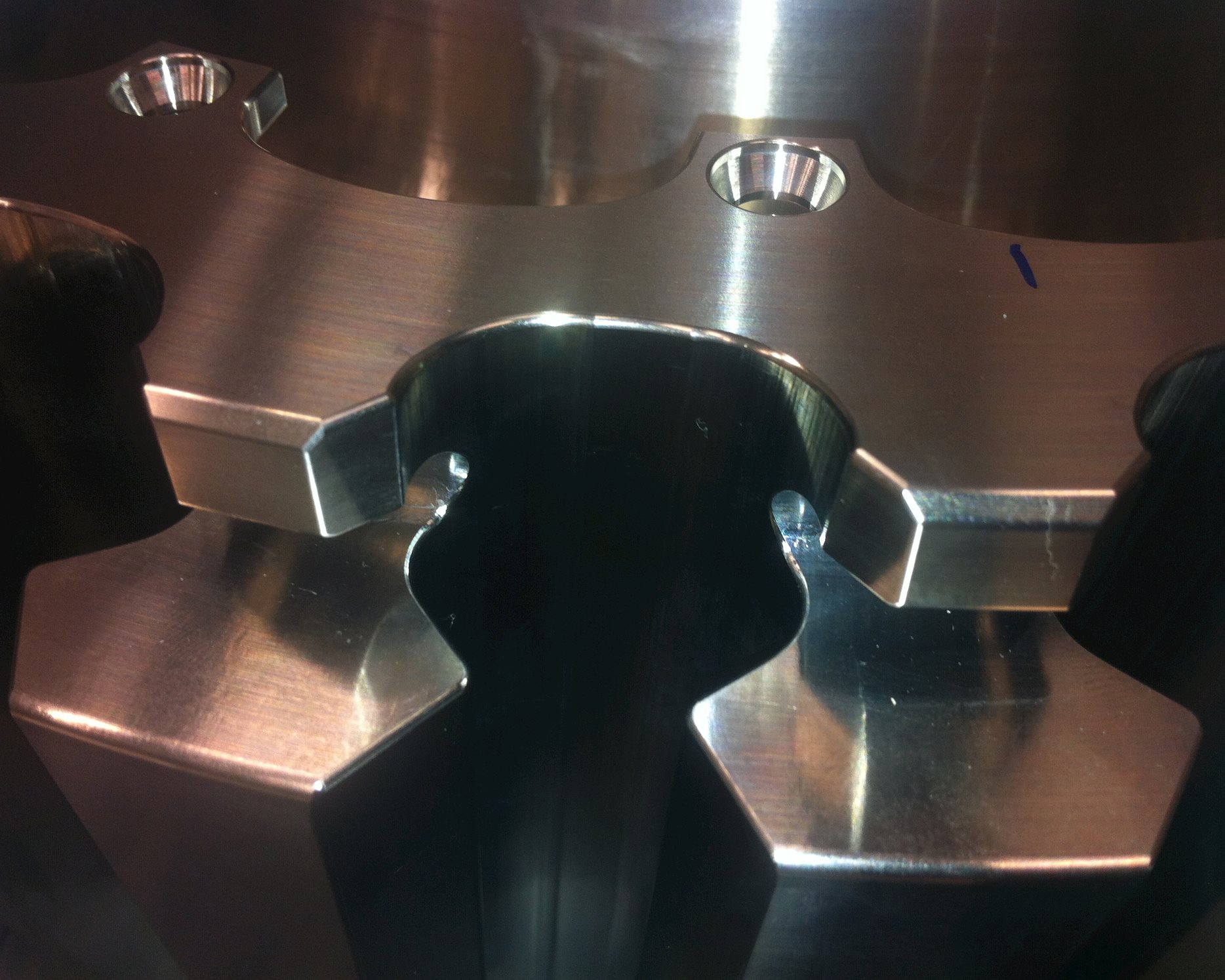
非回転構造部品に適用する標準的なバリ取りおよびプロファイル工具には、 45° および 60° の切れ刃を備えたコーティング処理された超硬ソリッド面取りエンドミルや、 45° および 60° の面取りの刃先交換式インサートを使用するツールが適用されます。
最も重要な加工用途向けに、切削工具メーカは、エッジをプロファイルし、特に穴の入口または出口でのバリを除去するために、カスタム設計されたツールを設計します。一部のツールはこれらの機能を組み合わせて、入口側と出口側の両方のバリを除去できます
これらのカスタムツールは、多くの場合、複雑な切削ジオメトリを特徴としています。最も革新のエッジ設計は、二次的なバリの生成を防ぐために設計されたリードイン角度とリードアウト角度が設定され、R形状でのエッジ面取りで加工されます。
特殊用途に適するツール開発は、刃先設計だけではありません。穴の入口または加工製品の上面バリやエッジのプロファイリング加工の場合、右捻じれのカットと右捻じれのカットの組み合わせが加工製品から被削材を除去するのに有効に機能し、最も効果的であることが研究によって明らかにされています。一方、加工製品底面の出口バリの場合は、右捻じれのカットと左捻じれのカットを組み合わせた方が最も効果的であり、この効果は切れ刃構成により切り屑が加工製品から離脱するためです。
他のアプリケーション分析では、穴の上部または入口のバリを除去するためにカスタム設計された MEP ツールは、貫通穴の底部または出口端のバリを除去するためのツールよりも長い工具寿命を維持することが実証されています。これは、穴の出口にアクセスするために加工製品の穴を貫通してアクセスするようにカスタム設計されたバリ取りツールが、穴の片側から加工することを意図したものよりもツールが長く、工具径が小さくなるためです。長く小径なツールは不安定で振動を発生しやすく、どちらも超硬ソリッドツールを欠損させたり破損させたりする可能性があります。その結果、ほとんどの製造工場では、穴の入口と出口のエッジのバリ取りに、両方に機能する 1 つのツールではなく、複数のツールを使用することを選択しています。
長く小さな工具径のツールでは、切削パラメータの選択に関しても注意が必要です。短くて強靭なツールは、振動やその他の問題をなくして速い作業が可能です。加工製品の形状や機能によっても違いが生じます。切削状態が安定しており、加工プロセスがスムーズで加工中断のない場合には、さらに積極的な切削パラメータを適用できます。一方で、MEP 加工プロセスパスを中断するアクセス穴などの加工製品形状では、ツールの摩耗を最小限に抑え、早期欠損を防止するために、より安全性を考慮した加工パラメータを適用する必要があります。
MEP プロセスツーリングの継続的な開発では、加工製品形状の加工プロセスとバリ取り加工を組み合わせたツールが適用されます。たとえば、MEP プロセスの切れ刃はエンドミルツールの上部側に配置されるため、加工穴の直径と入口面のバリの除去切削を同時に実施することが可能です。
大径穴やエッジ部を加工するために、工具メーカーは十分な大きさのブランクから、任意の必要サイズのツールを設計製作できます。ただし、領域サイズの小さい場合での限界はあります。現状では研削加工可能な最小半径は約 0.2 mm で、それに準じてリードイン角度とリードアウト角度が限定されます。
カスタム MEP プロセスツールには、特定の半径、面取り、角度、およびそれらの形状と機能の組み合わせがあります。通常はこれらのツールは、スクウェアショルダ切れ刃形状です。ただし、ボールノーズおよびロリポップツールは、ショルダ形状の MEP ツールへのアクセスを制限する加工要素の形状をプロファイル加工するためにも適用できます。これらのツールは 5 制御軸工作機械に適用され、複雑な加工製品プロファイルの製造プロセスをスキャンして、長い輪郭を持つエッジにR面を形成できます。
加工精度と加工均一性を最大限に高め、工作機械間の加工製品移動セットアップに要する時間を節約するために、通常、製造工場は実際の加工製品形状の生産プロセスの一部として MEP プロセスを応用します。
通常、バリ取り作業はすべての加工オペレーションが完了した後に行われます。CAM プログラムは、MEP ツールにすべての加工穴のバリ取りと鋭いエッジ切除加工を制御指示します。一部の MEP ツールは、加工製品のさまざまな加工穴のバリ取り加工に適用でき、一部のプロファイリングツールは、穴の底部や波形状輪郭の底部など、3 つまたは 4 つの異なる加工箇所または形状に適用できます。
エッジプロファイリングが指定の位置で適切な制御値で確実に実行されるようにするには、MEP プロセスを実行する前に、関連する穴または製品形状を定義または測定する必要があります。加工製品の指定公差が非常に厳しい場合、加工品の表面の位置が確実に測定されている場合には、プロセス内での測定が不要な場合があります。ただし、指定公差が大きい場合は、初回の加工後に加工製品のプロファイルのエッジまたは形状の位置を確定するための測定が必要です。
さらに、工具自体を測定して、加工製品に確実にプロファイル加工できるように位置精度を確認する必要があります。ツール半径値は非常に小さく、実用的には測定が容易でないため、ツール長さは CAM プログラムで設定と指定がされます。オペレータは、機械外の測定機やプリセッタを使用して工具長を確認することも、機械内でレーザー測定やタッチプローブを使用して工具長を確認することもできます。送り速度は、加工製品形状と測定されたツール寸法に基づいて算出決定されます。最も革新的なカスタムバリ取りツールは、径振れを含むツールプロファイルの公差値が 40 ミクロンになるように工具メーカによって 100% 測定保障されています。
バリ取りまたは面取り加工は、加工品質を第一に考え、最終仕上げパスとして考慮する必要があります。生産性は常に重要要素ですが、特に数十万ユーロの生産コストが必要な航空機産業コンポーネントの場合、ツールを最大限に活用して生産効率性を最大化にすることは、マイナスの影響と高価な影響を与える可能性があります。加工均一性、品質信頼性、不具合スクラップ低減が最も重要です。
機械化エッジプロファイリングは、さまざまな用途で製造企業に利益をもたらします。
ある事例では、製造企業はツインスピンドル工作機械による 303 ステンレス鋼材製品を製造していました。加工製品の生産量とバッチサイズが増大するにつれて、生産効率向上の必要性が高まりました。生産作業はバランスが悪く、多くの加工時間が費やされており、加工の 90% がメインスピンドルで実行され、加工品の下部のバリ取り処理を手作業で行うため、追加のセットアップのプロセスが必要でした。製造工場がカスタム設計の超硬ソリッド MEP ツールを工作機械のサブスピンドルに適用したところ、加工品のフランジ ボルト穴の両面側の倣い加工が同時に可能になりました。 2 つの主軸間の加工時間のバランスが均等化され、サイクルタイムが大幅に短縮されました。MEP ツールを適用すると、手作業のバリ取り処理の必要性がなくなり、余分なセットアップに要する時間が不要になります。
他の事例では、平坦エッジ面取りと放射エッジ面取りのどちらかの処理を選択する必要がありました。一部の加工製品には、いずれかのタイプのツーリングでエッジ処理するという指定の要件はありません。しかし、ある製造工場は、平坦面取りの代わりにアール面取りを適用すると、加工製品の寿命が平坦面取りした製品より 3 倍長くなることが確認されました。ツールの選択における一見小さな変更により、加工製品の品質が大幅に向上しました。
最後に、TiAl-4V ファン ディスクの航空機製造オペレーションによる、MEP コンタリングツールの適用例を示します。ある製造企業では、カムフィットホルダに保持された超硬ソリッド成型ツールを使用してタービンディスクを加工していました。 ディスクやスロット周辺のランダムな位置では仕上げ面精度が悪く、その課題は一貫性がなく、重大度や頻度も不安定でした。製造工場では、工具径 10 mm、10 枚刃のセンターカットロリポップタイプのコーティングされた 30 度右捻じれの超硬ソリッドエンドミルを使用していました。このツールの適用によって、表面仕上げ精度の課題を解決し、タービンディスクの両面をかなり短時間で仕上げることが可能になりました。
仕様基準に満たない、鋭いエッジやバリの残留した加工製品は、高価な不具合品とされることがあります。同様の事項は、航空機製造産業で顕著ですが、医療、エネルギー、その他の産業内の一部の重要なアプリケーションでも増加する傾向にあります。製造企業は、加工均一性があり、文書記録化可能で、生産コスト効率の高い、加工製品のバリ取りとエッジプロファイルを加工可能なプロセスを必要としています。機械化エッジプロファイリング (MEP) は、熟練者が実行しても、加工製品ごとに一貫性がなく、人件費、セットアップ費、部品処理費の面で生産コストが増大する手作業から置き換えることが可能なので、製造企業のニーズを満たすものになります。一部のエンドユーザーは、文書記録化および認証ができないため、手作業によるバリ取り作業をすでに禁止しています。
最も効率的で費用対効果の高い MEP は、エンジニアリング開発とアプリケーションの専門知識を融合させたものです。このようなトータルソリューションを提供する工具供給メーカは、航空機製造プロセス (および他の重要産業における同様のプロセス) の合理化に貢献し、革新的なレベルの加工プロセスと生産性を創造し続けます。